A kind of antiwear drag reducing agent for drilling fluid and preparation method thereof
A drag reducing agent and drilling fluid technology, applied in chemical instruments and methods, drilling compositions, etc., can solve problems such as economic losses, casualties, reduction in ROP, lubrication, and drag reduction efficiency, and achieve reduced Extreme pressure lubrication coefficient and mud cake adhesion coefficient, reduction of surface friction and wear, excellent effect of extreme pressure lubricity
- Summary
- Abstract
- Description
- Claims
- Application Information
AI Technical Summary
Problems solved by technology
Method used
Examples
preparation example Construction
[0028] A preparation method of an anti-wear drag reducing agent for drilling fluid, the method comprising the following steps:
[0029] (1) Under the sulfonation reaction conditions, according to the formula ratio in claim 2, the cottonseed oil and the sulfur powder mixture are reacted to obtain a sulfonated cottonseed oil compound with a sulfonated fatty acid salt content of ≥75%;
[0030] (2) Under the sulfonation reaction conditions, according to the formula ratio in claim 2, the vegetable oleic acid and the sulfur powder mixture are reacted to obtain a sulfonated oleic acid compound with a sulfonated fatty acid salt content of ≥75%;
[0031] (3) Under amidation reaction conditions, mixing and reacting the sulfonated oleic acid compound obtained in step (2) with diethanolamine to obtain a drag reducer main compound;
[0032] (4) Under the conditions of the neutralization reaction, combine the sulfonated cottonseed oil compound obtained in step (1), the drag reducer main compound obt...
Embodiment 1
[0041] Under the sulfonation reaction conditions at a temperature of 160°C, 28 parts by weight of cottonseed oil was reacted with 9 parts by weight of sulfur powder for 190 minutes to obtain a sulfonated cottonseed oil compound with a sulfonated fatty acid salt content of 77%. Parts of vegetable oleic acid reacted with 7 parts by weight of sulfur powder for 180 minutes to obtain a sulfonated oleic acid compound with a sulfonated fatty acid salt content of 75%; then under the conditions of amidation reaction, 35 parts by weight of sulfonated oleic acid were compounded And 3 parts by weight of diethanolamine at 145°C for 170 min amidation reaction to obtain the main drag reducer complex; finally, 36 parts by weight of the sulfonated cottonseed oil complex and 21 parts by weight of the drag reducer main complex Compound, 28 parts of kerosene, 15 parts of auxiliary materials and other materials are mixed for 130 minutes under normal temperature conditions to obtain the finished prod...
Embodiment 2
[0043] Under the condition of the sulfonation reaction at a temperature of 160°C, 29 parts by weight of cottonseed oil was reacted with 10 parts by weight of sulfur powder for 200 minutes to obtain a sulfonated cottonseed oil compound with a sulfonated fatty acid salt content of 79%. Parts of vegetable oleic acid was reacted with 8 parts by weight of sulfur powder for 190 minutes to obtain a sulfonated oleic acid compound with a sulfonated fatty acid salt content of 74%; then under the conditions of amidation reaction, 38 parts by weight of sulfonated oleic acid were compounded And 4 parts by weight of diethanolamine at 150°C for 210 min amidation reaction to obtain the main drag reducer complex; finally, 38 parts by weight of the sulfonated cottonseed oil complex and 20 parts by weight of the drag reducer main complex Compound, 26 parts of kerosene, 16 parts of auxiliary materials and other materials were mixed for 140 minutes under normal temperature conditions to obtain the f...
PUM
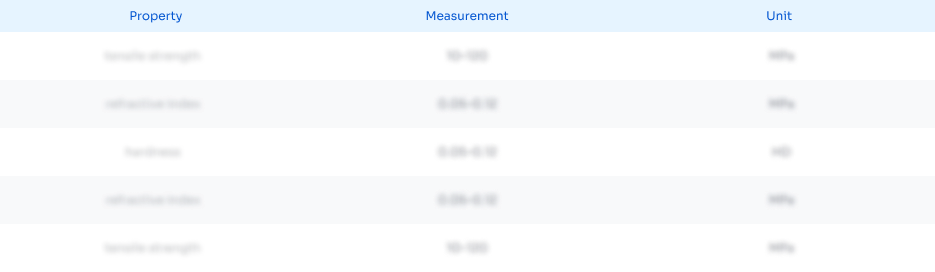
Abstract
Description
Claims
Application Information

- R&D Engineer
- R&D Manager
- IP Professional
- Industry Leading Data Capabilities
- Powerful AI technology
- Patent DNA Extraction
Browse by: Latest US Patents, China's latest patents, Technical Efficacy Thesaurus, Application Domain, Technology Topic, Popular Technical Reports.
© 2024 PatSnap. All rights reserved.Legal|Privacy policy|Modern Slavery Act Transparency Statement|Sitemap|About US| Contact US: help@patsnap.com