Liquid metal/polymer 3D printing ink and preparation method thereof
A liquid metal and 3D printing technology, applied in the field of materials, can solve problems such as uneven dispersion of liquid metal, only thin films can be prepared, and poor mechanical properties of materials
- Summary
- Abstract
- Description
- Claims
- Application Information
AI Technical Summary
Problems solved by technology
Method used
Image
Examples
Embodiment 1
[0039]Liquid metal (6.25g, 1mL) was mixed with tert-butyl acrylate (10mL), copper bromide (0.27mg), 2-bromo-N-(2-(((((8-hydroxyquinolin-2-yl) Methyl)amino)ethyl)-2-methylpropanamide (53mg) was uniformly mixed under the action of ultrasound in a cell disruptor (75W, 20min, in an ice bath). Ultrasound initiates polymerization, after NMR measurement of conversion rate, stop the reaction, add mass 1% initiator (phenylbis(2,4,6-trimethylbenzoyl) phosphorus oxide) and mass 3% A crosslinking agent (ethylene glycol dimethacrylate) was vibrated and mixed evenly to obtain a printing ink, and the ink was added to a 3D printer for photocuring printing.
Embodiment 2
[0041] Liquid metal (1.57g, 0.25mL) was mixed with butyl acrylate (5mL), copper bromide (0.1mg), 2-bromo-N-(2-(((((8-hydroxyquinolin-2-yl) Methyl)amino)ethyl)-2-methylpropanamide (2.66mg) was uniformly mixed under the action of ultrasound in a cell disruptor (75W, 20min, ice bath), and after 30min deoxygenation with nitrogen, placed in an ultrasonic cleaner, Turn on the ultrasound to initiate polymerization, and after the conversion rate is determined by NMR, the reaction is stopped, and a photoinitiator (phenylbis(2,4,6-trimethylbenzoyl) phosphine oxide) of 5% by mass is added to the mixed solution and a mass of 1 % cross-linking agent (ethylene glycol dimethacrylate) and shake and mix evenly to obtain printing ink, and add the ink into the 3D printer for photocuring printing.
Embodiment 3
[0043] Liquid metal (1.57g, 0.25mL) was mixed with methyl acrylate (5mL), copper bromide (0.1mg), 2-bromo-N-(2-(((((8-hydroxyquinolin-2-yl) Methyl)amino)ethyl)-2-methylpropanamide (2.66mg) was uniformly mixed under the action of ultrasound in a cell disruptor (75W, 20min, ice bath), and after 30min deoxygenation with nitrogen, placed in an ultrasonic cleaner, Turn on the ultrasound to initiate polymerization, and after the nuclear magnetic measurement conversion rate, stop the reaction, add a mass of 10% photoinitiator (phenylbis(2,4,6-trimethylbenzoyl) phosphorus oxide) and a mass of 3 % cross-linking agent (ethylene glycol dimethacrylate) and shake and mix evenly to obtain printing ink, and add the ink into the 3D printer for photocuring printing.
PUM
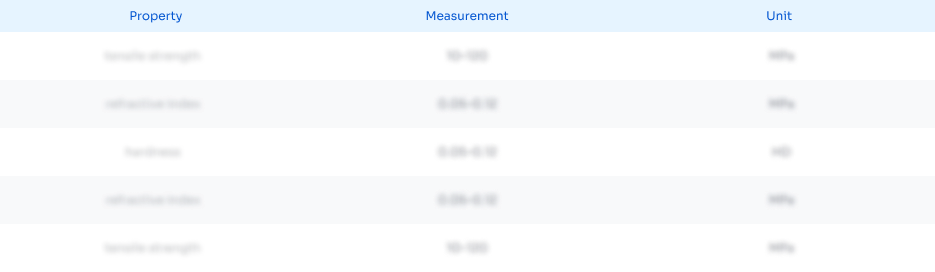
Abstract
Description
Claims
Application Information

- R&D Engineer
- R&D Manager
- IP Professional
- Industry Leading Data Capabilities
- Powerful AI technology
- Patent DNA Extraction
Browse by: Latest US Patents, China's latest patents, Technical Efficacy Thesaurus, Application Domain, Technology Topic, Popular Technical Reports.
© 2024 PatSnap. All rights reserved.Legal|Privacy policy|Modern Slavery Act Transparency Statement|Sitemap|About US| Contact US: help@patsnap.com