Novel magnetostrictive material designed according to FeGa-RFe2 magnetocrystalline anisotropy compensation principle and preparation method thereof
A technology of magnetostrictive materials and magnetocrystalline anisotropy, which is applied in the direction of material selection and device material selection for magnetostrictive devices, can solve problems such as high brittleness, high cost, and unfavorable machining, and achieve magnetostrictive The effect of high expansion and contraction performance
- Summary
- Abstract
- Description
- Claims
- Application Information
AI Technical Summary
Problems solved by technology
Method used
Image
Examples
Embodiment 1
[0050] Prepare 10g of the target component (Fe 83 Ga 17 ) 16 (TbFe 2 ) 1 Magnetostrictive alloy, the dosage is Fe: 7.953g, Ga: 2.031g, Tb: 0.016g. The mass percent purity of Fe, Ga and Tb is 99.99%.
[0051] It is smelted in a vacuum non-consumable arc melting furnace, and the vacuum is first evacuated to 4.0×10 -3 Pa, flushed into the furnace with argon gas, and then vacuumed to 2.0×10 -3 Pa, then filled with argon to a vacuum of 1×10 -1 Arc smelting after Pa again, with 140A electric current the raw material is melted into alloy and refined for 5 minutes, repeated smelting 4 times, obtains (Fe 83 Ga 17 ) 16 (TbFe 2 ) 1 Ingot;
[0052] Will (Fe 83 Ga 17 ) 16 (TbFe 2 ) 1 The ingot was wire-cut into 4 parts of similar size, and was ultrasonically cleaned with acetone for 8 minutes at a frequency of 40KHz, and then dried in an oven at 80°C for 15 minutes to obtain a clean (Fe 83 Ga 17 ) 16 (TbFe 2 ) 1 sample;
[0053] Will clean (Fe 83 Ga 17 ) 16 (TbFe ...
Embodiment 2
[0073] Prepare 10g of the target component (Fe 83 Ga 17 ) 4 (DyFe 2 ) 1 Magnetostrictive alloy, the dosage is Fe: 7.918g, Ga: 2.012g, Dy: 0.070g. The mass percent purity of Fe, Ga and Dy is 99.99%.
[0074] It is smelted in a vacuum non-consumable arc melting furnace, and the vacuum is first evacuated to 4.0×10 -3 Pa, flushed into the furnace with argon gas, and then vacuumed to 2.0×10 -3 Pa, then filled with argon to a vacuum of 1×10 -1 Arc smelting after Pa again, with 125A electric current, the raw material is melted into alloy and refined for 5 minutes, repeated smelting 4 times to obtain (Fe 83 Ga 17 ) 4 (DyFe 2 ) 1 Ingot;
[0075] Will (Fe 83 Ga 17 ) 4 (DyFe 2 ) 1 The ingot was wire-cut into 4 pieces of similar size, and was ultrasonically cleaned with acetone for 5 minutes at a frequency of 30KHz, and then dried in an oven at 120°C for 10 minutes to obtain a clean (Fe 83 Ga 17 ) 4 (DyFe 2 ) 1 sample;
[0076] Will clean (Fe 83 Ga 17 ) 4 (DyFe ...
Embodiment 3
[0083] Prepare 10g of the target component (Fe 83 Ga 17 ) 6 (HoFe 2 ) 1 Magnetostrictive alloy, the dosage is Fe: 7.934g, Ga: 2.021g, Ho: 0.045g. The mass percent purity of Fe, Ga and Ho is 99.99%.
[0084] It is smelted in a vacuum non-consumable arc melting furnace, and the vacuum is first evacuated to 4.0×10 -3 Pa, flushed into the furnace with argon gas, and then vacuumed to 2.0×10 -3 Pa, then filled with argon to a vacuum of 1×10 -1 Arc smelting after Pa again, with 120A electric current the raw material is melted into alloy and refined for 5 minutes, repeated smelting 4 times, obtains (Fe 83 Ga 17 ) 6 (HoFe 2 ) 1 Ingot;
[0085] Will (Fe 83 Ga 17 ) 6 (HoFe 2 ) 1 The ingot was wire-cut into 4 pieces of similar size, and was ultrasonically cleaned with acetone for 8 minutes at a frequency of 40KHz, and then dried in an oven at 100°C for 10 minutes to obtain a clean (Fe 83 Ga 17 ) 6 (HoFe 2 ) 1 sample;
[0086] Will clean (Fe 83 Ga 17 ) 6 (HoFe 2 ...
PUM
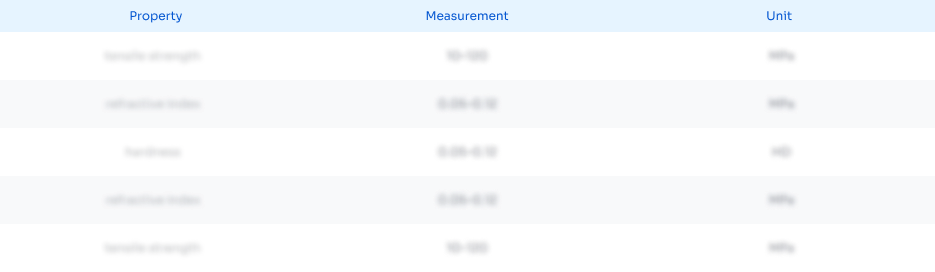
Abstract
Description
Claims
Application Information

- R&D
- Intellectual Property
- Life Sciences
- Materials
- Tech Scout
- Unparalleled Data Quality
- Higher Quality Content
- 60% Fewer Hallucinations
Browse by: Latest US Patents, China's latest patents, Technical Efficacy Thesaurus, Application Domain, Technology Topic, Popular Technical Reports.
© 2025 PatSnap. All rights reserved.Legal|Privacy policy|Modern Slavery Act Transparency Statement|Sitemap|About US| Contact US: help@patsnap.com