Resource utilization method of aluminum ash
A technology of resource utilization and aluminum ash, applied in the direction of improving process efficiency, can solve the problems of large waste, low recovery rate, large energy consumption, etc., and achieve the effects of low energy consumption, high production efficiency, and low equipment investment.
- Summary
- Abstract
- Description
- Claims
- Application Information
AI Technical Summary
Problems solved by technology
Method used
Image
Examples
Embodiment 1
[0032] After the aluminum ash is crushed by the jaw crusher, it is ball milled. The ball milling time is 15 minutes. After the ball milling, the 200-mesh sieve accounts for about 50%. After the ball milling, the aluminum ash is vibrated and screened. Metal aluminum in aluminum ash can be recovered, and its recovery rate is 95%. The aluminum ash under the sieve after ball milling is used as raw material, and the mass ratio of distilled water to aluminum ash is 3:1 for mixing. The mixing temperature is 65°C and the stirring time is 4h, filter the washed aluminum ash; put the sodium hydroxide solution and the washed aluminum ash in an autoclave to mix and stir at a liquid-solid ratio of 7:1, wherein the concentration of the sodium hydroxide solution is 130g / L, and the temperature is 140°C , the reaction pressure is 1.5MPa. After mixing and stirring for 6 hours, filter; mix and stir the mixed solution of sulfuric acid and hydrochloric acid with the aluminum ash after alkali leachi...
Embodiment 2
[0034] After the aluminum ash is crushed by the jaw crusher, it is ball milled. The ball milling time is 30 minutes. After the ball milling, the 200-mesh sieve accounts for about 55%. After the ball milling, the aluminum ash is vibrated and screened. Metal aluminum in aluminum ash can be recovered, and its recovery rate is 96%. The aluminum ash under the sieve after ball milling is used as raw material, and the mass ratio of distilled water to aluminum ash is 5:1 for mixing. The mixing temperature is 70°C, and the stirring time is 3h, filter to get washed aluminum ash; put sodium hydroxide, potassium hydroxide mixed solution and washed aluminum ash in an autoclave for mixing and stirring at a liquid-solid ratio of 6:1, wherein the concentration of the alkali solution is 120g / L , the temperature is 165°C, and the reaction pressure is 2.5MPa. After mixing and stirring for 5 hours, filter; mix and stir the sulfuric acid solution and the aluminum ash after alkali leaching at a liq...
Embodiment 3
[0036] After the aluminum ash is crushed by the jaw crusher, it is ball milled. The ball milling time is 45 minutes. After the ball milling, the 200 mesh sieve accounts for about 60%. After the ball milling, the aluminum ash is vibrated and screened. The ductility of metal aluminum is good. Metal aluminum in aluminum ash can be recovered, and its recovery rate is 98%. The aluminum ash under the sieve after ball milling is used as raw material, and the mass ratio of distilled water to aluminum ash is 7:1 for mixing. The mixing temperature is 85°C and the stirring time is After 2 hours, filter to obtain washed aluminum ash; put ammonia water and washed aluminum ash in an autoclave for mixing and stirring at a liquid-solid ratio of 8:1, the temperature is 195°C, and the reaction pressure is 0.8MPa. After mixing and stirring for 6 hours, filter; mix and stir sulfuric acid, nitric acid solution and aluminum ash after alkali leaching at a liquid-solid ratio of 4:1, in which the acid ...
PUM
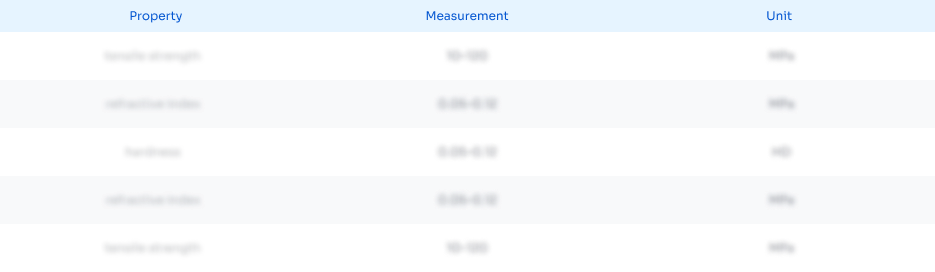
Abstract
Description
Claims
Application Information

- Generate Ideas
- Intellectual Property
- Life Sciences
- Materials
- Tech Scout
- Unparalleled Data Quality
- Higher Quality Content
- 60% Fewer Hallucinations
Browse by: Latest US Patents, China's latest patents, Technical Efficacy Thesaurus, Application Domain, Technology Topic, Popular Technical Reports.
© 2025 PatSnap. All rights reserved.Legal|Privacy policy|Modern Slavery Act Transparency Statement|Sitemap|About US| Contact US: help@patsnap.com