Heat-radiation coating material for ceramic kiln
A technology of ceramic kiln and thermal radiation, applied in the field of thermal radiation coatings for ceramic kilns, can solve the problems of coating performance influence, failure, and coating efficiency decline, and achieve the effects of small environmental impact, improved emissivity, and simple and convenient construction
- Summary
- Abstract
- Description
- Claims
- Application Information
AI Technical Summary
Problems solved by technology
Method used
Examples
Embodiment 1
[0016] Example 1 Zinc aluminum spinel powder 20%, manganese aluminum spinel powder 15%, ilmenite powder 10%, boron carbide 5%, iron oxide 3%, desiliconized zirconium powder 2%, binder 25%, yellow The dextrin is 0.5%, the rest is solvent, and the coating of the present invention can be prepared by mixing thoroughly.
Embodiment 2
[0018] Zinc-aluminum spinel powder 30%, manganese-aluminum spinel powder 5%, ilmenite powder 10%, boron carbide 5%, iron oxide 3%, desiliconized zirconium powder 2%, binder 25%, yellow dextrin 0.5 %, the rest is solvent, and the coating of the present invention can be prepared by mixing thoroughly.
Embodiment 3
[0020] Zinc aluminum spinel powder 25%, manganese aluminum spinel powder 10%, ilmenite powder 10%, boron carbide 5%, iron oxide 3%, desilication zirconium powder 2%, binder 25%, yellow dextrin 0.5 %, the rest is solvent, and the coating of the present invention can be prepared by mixing thoroughly.
PUM
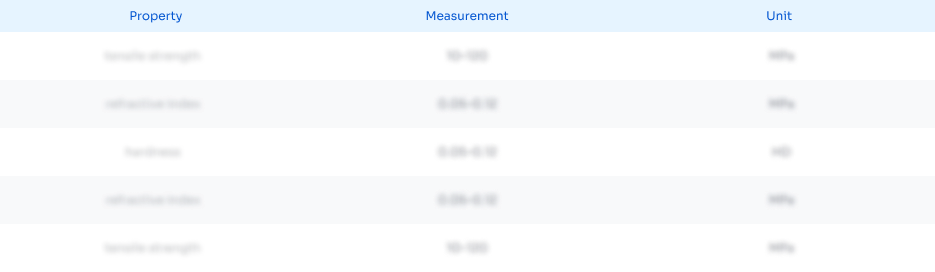
Abstract
Description
Claims
Application Information

- R&D Engineer
- R&D Manager
- IP Professional
- Industry Leading Data Capabilities
- Powerful AI technology
- Patent DNA Extraction
Browse by: Latest US Patents, China's latest patents, Technical Efficacy Thesaurus, Application Domain, Technology Topic, Popular Technical Reports.
© 2024 PatSnap. All rights reserved.Legal|Privacy policy|Modern Slavery Act Transparency Statement|Sitemap|About US| Contact US: help@patsnap.com