Method for recovering excess sodium hydroxide in tungsten smelting crude sodium tungstate solution
A technology of sodium hydroxide and crude sodium tungstate, which is applied in the field of tungsten smelting, can solve the problems of heating tube scaling, energy consumption reduction, and high energy consumption, and achieve the goals of preventing scaling, low environmental pressure, and low energy consumption Effect
- Summary
- Abstract
- Description
- Claims
- Application Information
AI Technical Summary
Problems solved by technology
Method used
Image
Examples
Embodiment 1
[0024] like figure 1 As shown, the recovery method of excess sodium hydroxide in the crude sodium tungstate solution of tungsten smelting is:
[0025] Step 1: Mix tungsten ore raw material and water in a volume ratio of 10:3 and add them into a ball mill for ball milling to obtain tungsten ore slurry, add sodium hydroxide solution to the tungsten ore slurry, and the added amount of the sodium hydroxide solution is the sodium hydroxide The content of sodium hydroxide in the solution is 1.0 times the content of tungsten trioxide in the tungsten ore raw material, and then the tungsten ore slurry added with the sodium hydroxide solution is pumped into a stirred medium-pressure reactor for alkaline pressure cooking to obtain Alkaline autoclaved slurry, the liquid-solid ratio during alkaline autoclave is generally 1 to 1.2:1, and the alkaline autoclaved slurry is press-filtered twice to obtain a crude sodium tungstate solution;
[0026] Wherein, the mass concentrations of sodium hy...
Embodiment 2
[0034] like figure 1 As shown, the recovery method of excess sodium hydroxide in the crude sodium tungstate solution of tungsten smelting is:
[0035] Step 1: Mix tungsten ore raw material and water in a volume ratio of 10:3 and add them into a ball mill for ball milling to obtain tungsten ore slurry, add sodium hydroxide solution to the tungsten ore slurry, and the added amount of the sodium hydroxide solution is the sodium hydroxide The content of sodium hydroxide in the solution is 1.2 times the content of tungsten trioxide in the tungsten ore raw material, and then the tungsten ore slurry added with the sodium hydroxide solution is pumped into a stirred medium-pressure reactor for alkaline pressure cooking to obtain Alkaline autoclaved slurry, the liquid-solid ratio during alkaline autoclave is generally 1 to 1.2:1, and the alkaline autoclaved slurry is press-filtered twice to obtain a crude sodium tungstate solution;
[0036] Wherein, the mass concentrations of sodium hy...
Embodiment 3
[0044] like figure 1 As shown, the recovery method of excess sodium hydroxide in the crude sodium tungstate solution of tungsten smelting is:
[0045] Step 1: Mix tungsten ore raw material and water in a volume ratio of 10:3 and add them into a ball mill for ball milling to obtain tungsten ore slurry, add sodium hydroxide solution to the tungsten ore slurry, and the added amount of the sodium hydroxide solution is the sodium hydroxide The content of sodium hydroxide in the solution is 1.4 times the content of tungsten trioxide in the tungsten ore raw material, and then the tungsten ore slurry added with the sodium hydroxide solution is pumped into a stirred medium-pressure reactor for alkaline pressure cooking to obtain Alkaline autoclaved slurry, the liquid-solid ratio during alkaline autoclave is generally 1 to 1.2:1, and the alkaline autoclaved slurry is press-filtered twice to obtain a crude sodium tungstate solution;
[0046] Wherein, the mass concentrations of sodium hy...
PUM
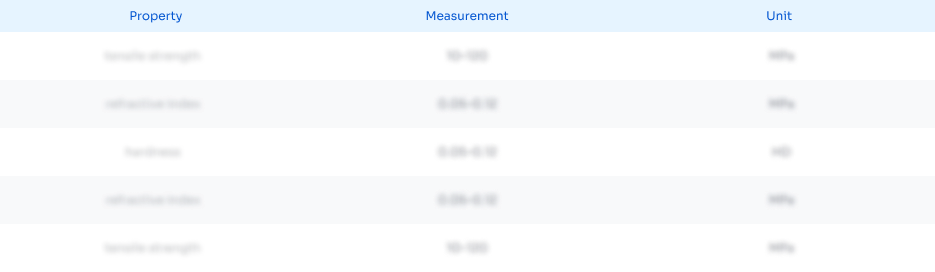
Abstract
Description
Claims
Application Information

- R&D Engineer
- R&D Manager
- IP Professional
- Industry Leading Data Capabilities
- Powerful AI technology
- Patent DNA Extraction
Browse by: Latest US Patents, China's latest patents, Technical Efficacy Thesaurus, Application Domain, Technology Topic, Popular Technical Reports.
© 2024 PatSnap. All rights reserved.Legal|Privacy policy|Modern Slavery Act Transparency Statement|Sitemap|About US| Contact US: help@patsnap.com