Preparation process for high-purity low-arsenic hydroxyethylidene diphosphonic acid
A technology of hydroxyethylene diphosphonic acid and preparation process, applied in the field of preparation of hydroxyethylene diphosphonic acid, can solve the problems of increasing impurities, increasing production cost, poor quality stability of amino trimethylene phosphonic acid and the like, and achieving The effect of reducing equipment investment, good stability and mild process control conditions
- Summary
- Abstract
- Description
- Claims
- Application Information
AI Technical Summary
Problems solved by technology
Method used
Examples
Embodiment 1
[0020] A preparation process of high-purity and low-arsenic hydroxyethylene diphosphonic acid uses phosphorus trichloride, acetic acid, and ammonium thioacetate as raw materials, and proceeds in accordance with the following steps:
[0021] The first step: first put 5500kg of acetic acid and 6kg of ammonium thioacetate into the reactor, under the condition of stirring, the temperature is controlled at 50~60°C and the pressure is below 200mmHg, and 2000 kg of phosphorus trichloride is added dropwise into the reactor, and then 8kg of sulfur Substitute ammonium acetate into the reactor, stop stirring, let it stand for 2 hours, then control the temperature at 40~50°C and the pressure below 200mmHg, add 5500kg of phosphorus trichloride to the reactor dropwise, after the dropwise addition, stir at a speed of 60 r / min for 1 Hours, and finally the temperature is slowly raised to 100°C. The hydrogen chloride gas produced in this process is absorbed by the hydrogen chloride absorber to p...
Embodiment 2
[0030] A preparation process of high-purity and low-arsenic hydroxyethylene diphosphonic acid uses phosphorus trichloride, acetic acid, and ammonium thioacetate as raw materials, and proceeds in accordance with the following steps:
[0031] Step 1: First, put 6000kg of acetic acid and 10kg of ammonium thioacetate into the reaction kettle, control the temperature at 50~60℃ and the pressure below 200mmHg under stirring conditions, add 2500 kg of phosphorus trichloride dropwise into the reaction kettle, and then add 6kg of sulfur Substitute ammonium acetate into the reactor, stop stirring, let it stand for 3 hours, then control the temperature at 40~50°C and the pressure below 200mmHg, add 5000 g of phosphorus trichloride to the reactor dropwise, after the addition is complete, stir at a speed of 50 r / min for 2 Hours, and finally the temperature is slowly raised to 100°C. The hydrogen chloride gas produced in this process is absorbed by the hydrogen chloride absorber to produce hy...
Embodiment 3
[0040] A preparation process of high-purity and low-arsenic hydroxyethylene diphosphonic acid uses phosphorus trichloride, acetic acid, and ammonium thioacetate as raw materials, and proceeds in accordance with the following steps:
[0041] The first step: first put 5800kg of acetic acid and 8kg of ammonium thioacetate into the reactor, under the condition of stirring, the temperature is controlled at 50~60°C and the pressure is below 200mmHg, and 2300 kg of phosphorus trichloride is added dropwise into the reactor, and then 10kg of sulfur Substitute ammonium acetate into the reactor, stop stirring, let it stand for 4 hours, then control the temperature at 40~50°C and the pressure below 200mmHg, add 5200 g of phosphorus trichloride to the reactor dropwise, after the addition is completed, stir at a speed of 55 r / min for 3 Hours, and finally the temperature is slowly raised to 100°C. The hydrogen chloride gas produced in this process is absorbed by the hydrogen chloride absorber...
PUM
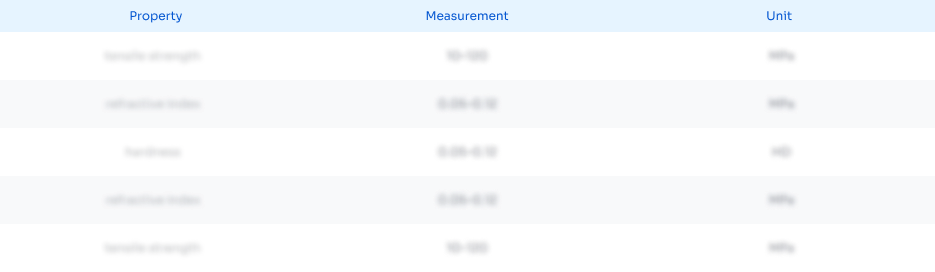
Abstract
Description
Claims
Application Information

- R&D Engineer
- R&D Manager
- IP Professional
- Industry Leading Data Capabilities
- Powerful AI technology
- Patent DNA Extraction
Browse by: Latest US Patents, China's latest patents, Technical Efficacy Thesaurus, Application Domain, Technology Topic, Popular Technical Reports.
© 2024 PatSnap. All rights reserved.Legal|Privacy policy|Modern Slavery Act Transparency Statement|Sitemap|About US| Contact US: help@patsnap.com