Commutation torque ripple restraining method and system for brushless DC (Direct Current) motor driving system
A brushed DC motor and drive system technology, applied in the field of mechanical engineering, can solve the problems of sensitive motor parameters, lack of universal applicability, and difficulty in determining the commutation time.
- Summary
- Abstract
- Description
- Claims
- Application Information
AI Technical Summary
Problems solved by technology
Method used
Image
Examples
Embodiment 1
[0073] 1 Mechanism Analysis of Commutation Torque Ripple
[0074] Two-two conduction three-phase six-state brushless DC motor during commutation, because the stator winding is an inductive element, its current cannot change abruptly. After commutation starts, the off-phase current will not drop to zero immediately, and the on-phase current will not rise to a stable value immediately, that is, the current waveform will not be a standard rectangular wave but a trapezoidal shape during commutation. Only through a special control method or only when certain conditions are met can the drop rate of the off-phase current be equal to the rise rate of the access phase current, otherwise, it will inevitably cause the pulsation of the non-commutation current in the winding, resulting in a commutation switch. torque ripple.
[0075] 1.1 Equivalent circuit analysis of commutation process
[0076] figure 1 It is the equivalent circuit diagram of the brushless DC motor and the ideal thre...
PUM
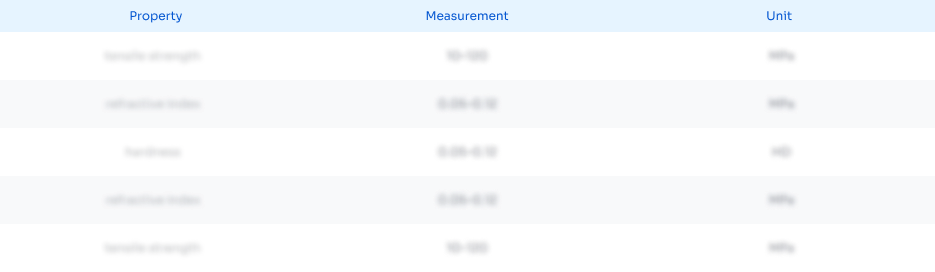
Abstract
Description
Claims
Application Information

- R&D
- Intellectual Property
- Life Sciences
- Materials
- Tech Scout
- Unparalleled Data Quality
- Higher Quality Content
- 60% Fewer Hallucinations
Browse by: Latest US Patents, China's latest patents, Technical Efficacy Thesaurus, Application Domain, Technology Topic, Popular Technical Reports.
© 2025 PatSnap. All rights reserved.Legal|Privacy policy|Modern Slavery Act Transparency Statement|Sitemap|About US| Contact US: help@patsnap.com