Film sintered electromagnetic wire induction heating bonding system and method for making the electromagnetic wire
A technology of induction heating and induction heating devices, which is applied in the direction of cable/conductor manufacturing, circuits, electrical components, etc., can solve problems such as troublesome operation, affecting production progress and production efficiency, and unfavorable stable quality of electromagnetic wires, and achieves simple and convenient operation, Improved production efficiency and stable product quality
- Summary
- Abstract
- Description
- Claims
- Application Information
AI Technical Summary
Problems solved by technology
Method used
Image
Examples
Embodiment Construction
[0024] The present invention will be described in detail below:
[0025] As shown in the accompanying drawings, a thin film sintering electromagnetic wire induction heating bonding system includes a wire rack, a straightening device for straightening the conductor, a polishing machine for removing burrs on the conductor, and Water washing device for cleaning conductors, air-drying device for air-drying conductors, wrapping device for wrapping film on conductors, crawler traction device for pulling magnet wires Heating induction heating device 1, rolling device 2 for rolling the heated electromagnetic wire, oven 3 for consolidating and heating the rolled electromagnetic wire, cooling the baked electromagnetic wire Water-cooled drying device, wire take-up machine.
[0026] The induction heating device 1 includes an induction heating device body 4 capable of moving back and forth, and a high-frequency induction heating coil body 5 fixedly arranged on the induction heating device...
PUM
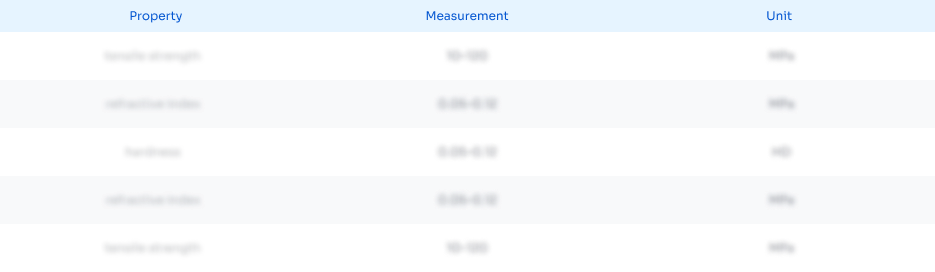
Abstract
Description
Claims
Application Information

- Generate Ideas
- Intellectual Property
- Life Sciences
- Materials
- Tech Scout
- Unparalleled Data Quality
- Higher Quality Content
- 60% Fewer Hallucinations
Browse by: Latest US Patents, China's latest patents, Technical Efficacy Thesaurus, Application Domain, Technology Topic, Popular Technical Reports.
© 2025 PatSnap. All rights reserved.Legal|Privacy policy|Modern Slavery Act Transparency Statement|Sitemap|About US| Contact US: help@patsnap.com