Production method of red mud filler
A production method, red mud technology, applied in fibrous filler, dyeing physical treatment, dyeing low-molecular organic compound treatment, etc., can solve the problems of particle size not meeting the requirements, high iron content in powder, dust pollution, etc. Achieve the effect of low production cost, less environmental pollution and no secondary pollution
- Summary
- Abstract
- Description
- Claims
- Application Information
AI Technical Summary
Problems solved by technology
Method used
Examples
Embodiment 1
[0020] The grinder used in this example adopts the wet method vertical stirring grinder produced by Kunshan Miyou Crushing Equipment Co., Ltd.; the flash dryer adopts the XSG series rotary flash dryer produced by Changzhou Maijieke Drying Equipment Co., Ltd.; The CM type impact ultra-fine grinding machine produced by the Powder Engineering Center of Xianyang Non-metallic Mineral Research and Design Institute; the classifier adopts the FW series airflow classifier produced by Qingdao Micron Powder Technology Equipment Co., Ltd.; the modification machine adopts Qingdao Zhongyi PSC powder surface modification machine equipped with heating device and spray nozzle produced by Machinery Equipment Co., Ltd.
[0021] (1) Wet grinding: send the 80-120 mesh coarse red mud slurry from the red mud classification process into the grinder, and perform wet grinding to 1250-5000 mesh to obtain fine red mud slurry;
[0022] (2) Dehydration: Put the fine red mud slurry into a plate and frame fi...
Embodiment 2
[0028] The equipment is the same as in Example 1.
[0029] (1) Wet grinding: send the 80-120 mesh coarse red mud slurry from the red mud classification process into the grinder, and perform wet grinding to 1250-5000 mesh to obtain fine red mud slurry;
[0030] (2) Dehydration: Put the fine red mud slurry into a plate and frame filter press for press dehydration, and press it into a red mud filter cake with a water content of less than 25%; the temperature of the press filter is normal temperature, and the pressure is 0.6-0.8 MPa;
[0031] (3) Drying: send the filter cake into a flash dryer for pulverization and drying, the drying temperature is 500°C, and the drying time is 25 minutes to obtain a powder with a moisture content of less than 0.5%;
[0032] (4) Grinding: the powder is ultrafinely ground using an impact ultrafine pulverizer to obtain ultrafine powder of 1250 to 6000 mesh;
[0033] (5) Classification: adopt a classifier to classify the superfine mill discharge to...
Embodiment 3
[0036] The equipment is the same as in Example 1.
[0037] (1) Wet grinding: send the 80-120 mesh coarse red mud slurry from the red mud classification process into the grinder, and perform wet grinding to 1250-5000 mesh to obtain fine red mud slurry;
[0038] (2) Dehydration: Put the fine red mud slurry into a plate and frame filter press for press dehydration, and press it into a red mud filter cake with a water content of less than 25%; the temperature of the press filter is normal temperature, and the pressure is 0.6-0.8 MPa;
[0039] (3) Drying: send the filter cake into a flash dryer for pulverization and drying, the drying temperature is 600°C, and the drying time is 20 minutes to obtain a powder with a moisture content of less than 0.5%;
[0040] (4) Grinding: the powder is ultrafinely ground using an impact ultrafine pulverizer to obtain ultrafine powder of 1250 to 6000 mesh;
[0041] (5) Classification: adopt a classifier to classify the superfine mill discharge to...
PUM
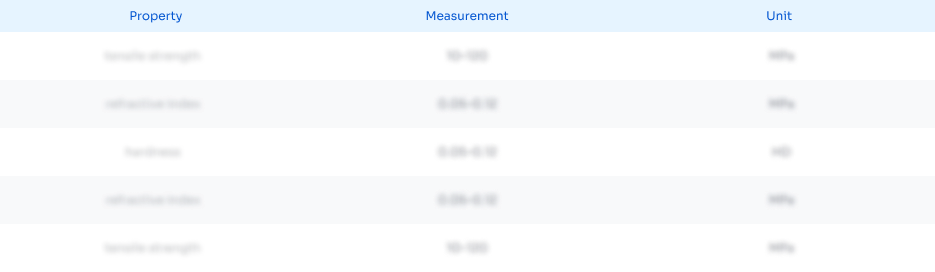
Abstract
Description
Claims
Application Information

- R&D Engineer
- R&D Manager
- IP Professional
- Industry Leading Data Capabilities
- Powerful AI technology
- Patent DNA Extraction
Browse by: Latest US Patents, China's latest patents, Technical Efficacy Thesaurus, Application Domain, Technology Topic, Popular Technical Reports.
© 2024 PatSnap. All rights reserved.Legal|Privacy policy|Modern Slavery Act Transparency Statement|Sitemap|About US| Contact US: help@patsnap.com