Unit of recovering flue gas waste heat and dust in reclaimed copper refining
A waste heat recovery device, dust recovery technology, applied in waste heat treatment, lighting and heating equipment, use of liquid separation agent, etc., can solve problems affecting stable production, high energy consumption, environmental pollution, etc., to improve heat recovery rate, protect Spontaneous combustion, environmental protection, and the effect of improving smelting yield
- Summary
- Abstract
- Description
- Claims
- Application Information
AI Technical Summary
Problems solved by technology
Method used
Image
Examples
Embodiment 1
[0062] A recycling device for waste heat and dust in flue gas from secondary copper refining, including a waste heat recovery device and a dust recovery device;
[0063] The waste heat recovery device is composed of a countercurrent heat exchange waste heat boiler A1, a countercurrent heat exchange waste heat boiler B2 and a countercurrent heat exchange waste heat boiler working fluid preheater 3;
[0064] The dust recovery device is composed of a water washing tower 4, a liquid film scrubber 5, a mist catcher 6, an induced draft fan 7, a sedimentation filter A8, and a sedimentation filter B9;
[0065] The waste heat recovery device and the dust recovery device are sequentially connected through pipelines or pipe fittings. The recovery and utilization method of waste heat and dust in the flue gas includes the following steps:
[0066] ①. Primary recovery of waste heat
[0067] The 1350°C flue gas from the secondary copper refining furnace enters the countercurrent heat exchan...
Embodiment 2
[0082] According to the recovery and utilization device of waste heat and dust in the secondary copper refining flue gas of embodiment 1, the difference is:
[0083] The waste heat recovery device used in steps ①, ② and ③ is the countercurrent heat exchange waste heat boiler A1, the countercurrent heat exchange waste heat boiler B2 and the countercurrent heat exchange waste heat boiler working medium preheater 3, and the heat exchange between the flue gas and the boiler working medium is uniform. The three-pipe countercurrent heat exchange method is adopted. The heat exchange device is composed of three straight tubes with different diameters. The flue gas goes through the central tube and the outer ring gap, and the waste heat recovery working fluid goes through the inner ring gap tube. The two flow directions are opposite. Realize countercurrent heat exchange.
[0084] Waste heat recovery rate ≥ 95%. The tail gas discharged meets the emission standard stipulated by the stat...
Embodiment 3
[0086] According to the recovery and utilization device of waste heat and dust in the secondary copper refining flue gas of embodiment 1, the difference is:
[0087] The waste heat recovery device used in step ① is the countercurrent heat exchange waste heat boiler A1. The heat exchange between the flue gas and the boiler waste heat recovery working fluid adopts the double-pipe countercurrent heat exchange method. The heat exchange device consists of several two straight tubes with different diameters The tube set configuration is combined, the flue gas goes through the central tube, and the waste heat recovery working medium goes through the ring gap tube, and the flow directions of the two are opposite to realize countercurrent heat exchange.
[0088] The waste heat recovery device used in steps ② and ③ uses a three-tube countercurrent heat exchange method for the heat exchange between the flue gas and the boiler working fluid in the countercurrent heat exchange waste heat bo...
PUM
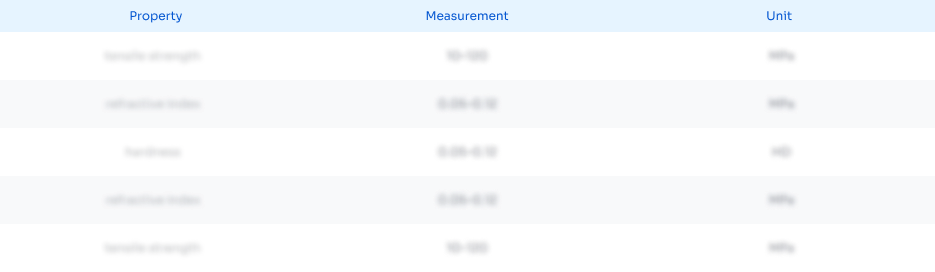
Abstract
Description
Claims
Application Information

- R&D
- Intellectual Property
- Life Sciences
- Materials
- Tech Scout
- Unparalleled Data Quality
- Higher Quality Content
- 60% Fewer Hallucinations
Browse by: Latest US Patents, China's latest patents, Technical Efficacy Thesaurus, Application Domain, Technology Topic, Popular Technical Reports.
© 2025 PatSnap. All rights reserved.Legal|Privacy policy|Modern Slavery Act Transparency Statement|Sitemap|About US| Contact US: help@patsnap.com