Preparation method of flame-retardant, impact-resistant and high-fluidity chloroethylene-based special resin
A high-fluidity, vinyl chloride technology, applied in the preparation of flame-retardant, high-fluidity vinyl chloride-based special resins, and in the field of impact resistance, it can solve the problems of high water absorption, achieve high gloss, simple process, and excellent fluidity Effect
- Summary
- Abstract
- Description
- Claims
- Application Information
AI Technical Summary
Problems solved by technology
Method used
Image
Examples
Embodiment 1
[0031] Add 100 g deionized water, 1 g potassium persulfate, 4 g alkylphenol polyoxyethylene ether emulsifier CO, 2 g sodium lauryl sulfate, 2 g tert-butyl alcohol, 0.1 g polyvinyl alcohol, 100 g rubber seed oil and 3 g divinylbenzene. Stir at 30°C for 15 minutes to obtain a latex rubber emulsion; then, raise the temperature of the reaction system to 60°C, heat the reaction for 2 hours, then cool to room temperature to obtain a soft monomer core emulsion.
[0032] Add 100 g of vinyl chloride (351.1), 50 g of styrene, 100 g of the above-mentioned soft monomer emulsion, 1 g of peroxydicarbonate, 100 g of deionized water, and 0.1 g carboxycellulose. After stirring evenly, gradually increase the temperature of the system to 50°C, heat-preserve and pressure-hold the reaction until the pressure of the system drops significantly, continue the heat-retaining reaction for 1 hour, and cool the system to room temperature to obtain a flame-retardant, impact-resistant, high-flow performanc...
Embodiment 2
[0034] Add 1000 g deionized water, 10 g ammonium persulfate, 12 g alkylphenol polyoxyethylene ether emulsifier OP, 9 g sodium dodecylbenzenesulfonate, 5 g lauryl alcohol, 1 g gelatin, 0.5 polyvinyl alcohol, 1000 g isooctyl acrylate and 25 g ethylene glycol diacrylate (diene acrylate). Stir at 30° C. for 10 minutes to obtain an isooctyl acrylate emulsion; then, raise the temperature of the reaction system to 70° C., keep it warm for 2 hours, then cool to room temperature to obtain a soft monomer core emulsion.
[0035]Add 500 g of vinyl chloride, 50 g of vinylidene chloride, 800 g of styrene, 1000 g of the above soft monomer emulsion, 5 g of dicumyl peroxide, 5 g of g peroxydicarbonate, 1000 g deionized water and 1 g carboxylated cellulose. After stirring evenly, gradually increase the temperature of the system to 60°C, heat-preserve and press-hold the reaction until the pressure of the system drops significantly, continue the heat-retaining reaction for 1 hour, and cool the s...
Embodiment 3
[0037] Add 1000 g deionized water, 10 g ammonium persulfate, 10 g alkylphenol polyoxyethylene ether emulsifier NP, 10 g sodium lauryl sulfate, 0.5 g Sodium alginate, 0.5 polyvinyl alcohol, 800 g butyl acrylate and 20 g ethylene glycol diacrylate (diene acrylate). Stir at 30°C for 30 minutes to obtain a butyl acrylate emulsion; then, raise the temperature of the reaction system to 90°C, keep the temperature for 2 hours, then cool to room temperature to obtain a soft monomer core emulsion.
[0038] Add 500 g vinyl chloride, 50 g vinylidene chloride, 800 g styrene, 1000 g of the above soft monomer emulsion, 5 g peroxydicarbonate, 5 g Dicumyl peroxide, 0.5 g mercaptoethanol, 1000 g deionized water and 1 g carboxylated cellulose. After stirring evenly, gradually raise the temperature of the system to 40°C, heat-preserve and pressure-hold the reaction until the pressure of the system drops significantly, continue the heat-retaining reaction for 1 hour, and cool the system to room t...
PUM
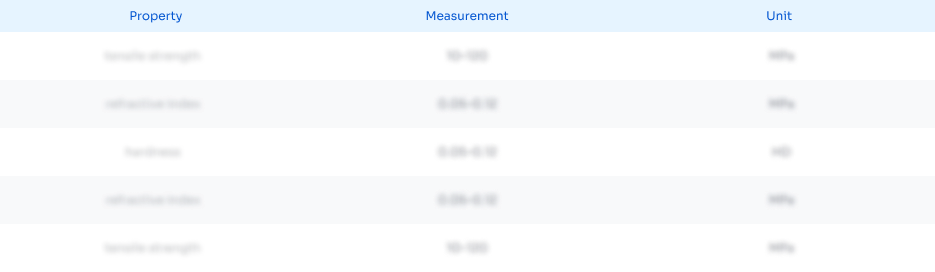
Abstract
Description
Claims
Application Information

- R&D
- Intellectual Property
- Life Sciences
- Materials
- Tech Scout
- Unparalleled Data Quality
- Higher Quality Content
- 60% Fewer Hallucinations
Browse by: Latest US Patents, China's latest patents, Technical Efficacy Thesaurus, Application Domain, Technology Topic, Popular Technical Reports.
© 2025 PatSnap. All rights reserved.Legal|Privacy policy|Modern Slavery Act Transparency Statement|Sitemap|About US| Contact US: help@patsnap.com