Manufacturing method for ultrathin embossment protective case
A manufacturing method and technology for a protective case, which are applied in the field of ultra-thin embossed protective shell manufacturing, can solve the problem that the surface embossing effect cannot be changed in a short period of time and low cost, it is difficult to realize the production of ultra-thin embossed leather cases/protective shells, and it is difficult to achieve accurate Manufacturing and other problems, to achieve the effect of increasing the appearance aesthetics, excellent high temperature suction performance, and high molding efficiency
- Summary
- Abstract
- Description
- Claims
- Application Information
AI Technical Summary
Problems solved by technology
Method used
Image
Examples
Embodiment
[0044] Example: see Figure 1 to Figure 7 , a method for manufacturing an ultra-thin embossed protective case provided in this embodiment, which includes the following steps:
[0045] (1) Prepare the plastic-absorbing composite material 7;
[0046] (2) Prepare a relief concave mold, and form the plastic-absorbing composite material 7 into a sheet material 8 uniformly distributed on the surface with a plurality of concave positions matching the outline of the product to be protected;
[0047] (3) Use punching equipment to punch the sheet material 8 at the position corresponding to the concave position, so as to form a plurality of semi-finished shells 10 that match the outline of the product to be protected;
[0048] (4) According to the position of the exposed part of the side wall of the product to be protected, the semi-finished shell 10 is trimmed and shaped so that the edge forms a depression that exposes the exposed part of the side wall of the product to be protected; ...
PUM
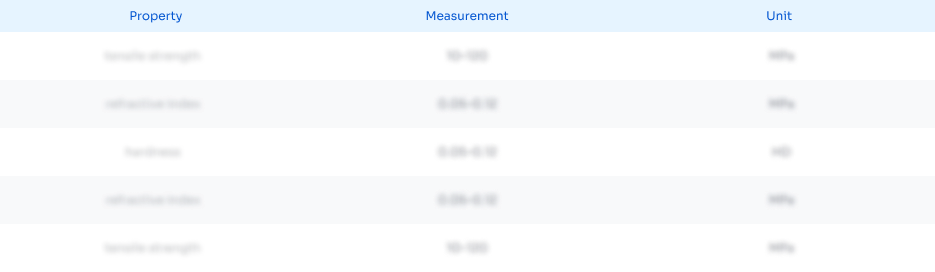
Abstract
Description
Claims
Application Information

- Generate Ideas
- Intellectual Property
- Life Sciences
- Materials
- Tech Scout
- Unparalleled Data Quality
- Higher Quality Content
- 60% Fewer Hallucinations
Browse by: Latest US Patents, China's latest patents, Technical Efficacy Thesaurus, Application Domain, Technology Topic, Popular Technical Reports.
© 2025 PatSnap. All rights reserved.Legal|Privacy policy|Modern Slavery Act Transparency Statement|Sitemap|About US| Contact US: help@patsnap.com