Method for extracting vanadium from stone coal containing vanadium
A vanadium stone and content technology, applied in the field of vanadium extraction, can solve the problems of complex vanadium extraction process from stone coal, harsh equipment requirements, ineffective use of acid, etc., and achieve simplified vanadium extraction process from stone coal, strong continuous production, and Simple effect of vanadium extraction process from coal
- Summary
- Abstract
- Description
- Claims
- Application Information
AI Technical Summary
Problems solved by technology
Method used
Image
Examples
Embodiment 1
[0025] A method for extracting vanadium from vanadium-containing stone coal, the specific steps of the method are:
[0026] Step 1. Blank roasting
[0027] First crush the vanadium-containing stone coal to a particle size of <3mm, then raise the temperature of the crushed vanadium-containing stone coal to 700-800°C at a rate of 6-30°C / min, roast at a constant temperature for 1-1.5h, and cool to room temperature , and then ground to a particle size of less than 0.074mm, accounting for 65~85wt% vanadium-containing stone coal powder ore.
[0028] Step two, one-stage acid leaching
[0029] Firstly, the leaching agent and the vanadium-containing pulverized coal ore are stirred and leached for 1-3 hours at 80-95°C according to the liquid-solid mass ratio of (2.5-4)︰1, and then a stage of solid-liquid separation is carried out to obtain a stage of leachate and One-stage leaching residue; among them: one-stage leaching solution is directly used for subsequent purification and enrich...
Embodiment 2
[0036] A method for extracting vanadium from vanadium-containing stone coal, the specific steps of the method are:
[0037] Step 1. Blank roasting
[0038]First crush the vanadium-containing stone coal to a particle size of <3mm, then raise the temperature of the crushed vanadium-containing stone coal to 800-900°C at a rate of 6-30°C / min, roast at a constant temperature for 1.5-2 hours, and cool to room temperature. Then grind until the particle size is less than 0.074mm, accounting for 65~85wt% vanadium-containing stone coal powder ore.
[0039] Step two, one-stage acid leaching
[0040] Firstly, the leaching agent and the vanadium-containing pulverized coal ore are stirred and leached for 2-4 hours at 90-100°C according to the liquid-solid mass ratio of (3.5-5)︰1, and then a stage of solid-liquid separation is carried out to obtain a stage of leachate and One-stage leaching residue; among them: one-stage leaching solution is directly used for subsequent purification and en...
PUM
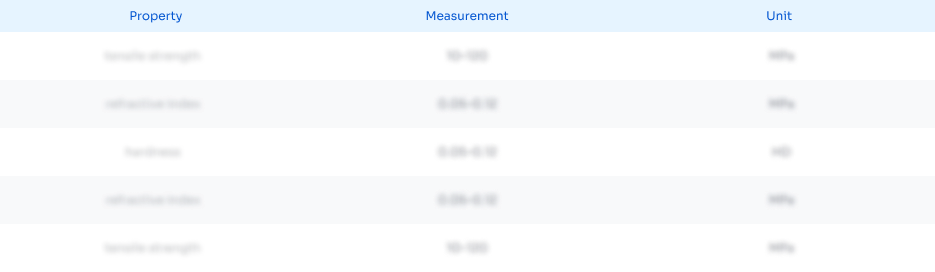
Abstract
Description
Claims
Application Information

- R&D
- Intellectual Property
- Life Sciences
- Materials
- Tech Scout
- Unparalleled Data Quality
- Higher Quality Content
- 60% Fewer Hallucinations
Browse by: Latest US Patents, China's latest patents, Technical Efficacy Thesaurus, Application Domain, Technology Topic, Popular Technical Reports.
© 2025 PatSnap. All rights reserved.Legal|Privacy policy|Modern Slavery Act Transparency Statement|Sitemap|About US| Contact US: help@patsnap.com