Method for lixiviating molybdenum from roasted molybdenite
A molybdenum calcining and leaching technology, applied in the field of hydrometallurgy, can solve the problems of affecting the leaching rate of molybdenum, cumbersome process methods for recovering molybdenum, troublesome treatment of ammonia leaching slag, etc.
- Summary
- Abstract
- Description
- Claims
- Application Information
AI Technical Summary
Problems solved by technology
Method used
Image
Examples
Embodiment 1
[0024] The method for leaching molybdenum from molybdenum calcine in the present embodiment comprises the following steps:
[0025] Step 1, after molybdenum calcined sand, ammonium carbonate and deionized water are mixed uniformly in a mass ratio of 1:0.75:2.5, the temperature is stirred at 80°C for 60 minutes to obtain a suspension; the molybdenum calcined sand contains molybdenum The mass percentage content is 63%;
[0026] Step 2, filtering the suspension described in step 1 to obtain filter cake and filtrate;
[0027] Step 3, adopting the ammoniacal liquor that mass percent concentration is 26% to wash the filter cake described in step 2, then the ammoniacal liquor after washing is mixed with the filtrate described in step 2, obtains mixed solution; The consumption of described ammoniacal liquor is molybdenum 0.9 times the quality of calcined sand, and the number of washings is 2 times;
[0028] Step 4, using liquid ammonia or ammonia water with a mass percentage concent...
Embodiment 2
[0034] The method for leaching molybdenum from molybdenum calcine in the present embodiment comprises the following steps:
[0035] Step 1, after molybdenum calcined sand, ammonium carbonate and deionized water are mixed uniformly by mass ratio 1:0.82:3, stir 70min under the condition that temperature is 70 ℃, obtain suspension liquid; The molybdenum in described molybdenum calcined sand The mass percentage content is 63%;
[0036] Step 2, filtering the suspension described in step 1 to obtain filter cake and filtrate;
[0037] Step 3, adopting the ammoniacal liquor that mass percentage concentration is 28% to wash the filter cake described in step 2, then the ammoniacal liquor after washing is mixed with the filtrate described in step 2, obtains mixed solution; The consumption of described ammoniacal liquor is molybdenum 0.8 times the quality of calcined sand, and the number of washings is 1 time;
[0038] Step 4: Adjust the pH value of the mixed solution described in step ...
Embodiment 3
[0044] The method for leaching molybdenum from molybdenum calcine in the present embodiment comprises the following steps:
[0045] Step 1, after molybdenum calcined sand, ammonium carbonate and deionized water are mixed uniformly by mass ratio 1:0.66:3, stir 40min under the condition that temperature is 90 ℃, obtain suspension liquid; The molybdenum in described molybdenum calcined sand The mass percentage content is 62.4%;
[0046] Step 2, filtering the suspension described in step 1 to obtain filter cake and filtrate;
[0047] Step 3, adopting the ammoniacal liquor that mass percentage concentration is 25% to wash the filter cake described in step 2, then the ammoniacal liquor after washing is mixed with the filtrate described in step 2, obtains mixed solution; The consumption of described ammoniacal liquor is molybdenum 0.6 times the quality of calcined sand, and the number of washings is 2 times;
[0048] Step 4: Adjust the pH value of the mixed solution described in st...
PUM
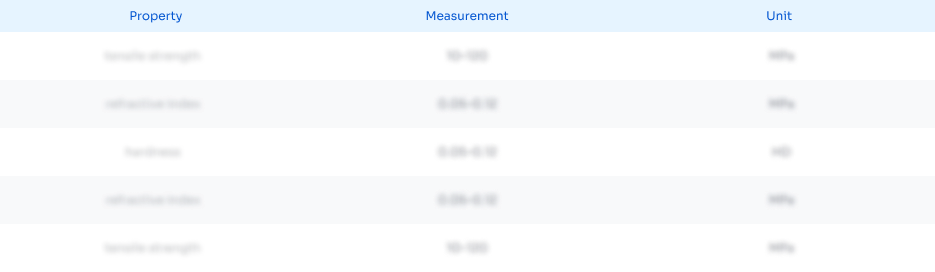
Abstract
Description
Claims
Application Information

- R&D
- Intellectual Property
- Life Sciences
- Materials
- Tech Scout
- Unparalleled Data Quality
- Higher Quality Content
- 60% Fewer Hallucinations
Browse by: Latest US Patents, China's latest patents, Technical Efficacy Thesaurus, Application Domain, Technology Topic, Popular Technical Reports.
© 2025 PatSnap. All rights reserved.Legal|Privacy policy|Modern Slavery Act Transparency Statement|Sitemap|About US| Contact US: help@patsnap.com