Baffling fin casting plate-type air pre-heater
An air preheater and plate-type technology, which is applied in the field of high-efficiency heat exchange and energy-saving heat exchange equipment, can solve the problems of reducing heat exchange efficiency, unfavorable heat exchange, and increasing thermal resistance, so as to achieve good heat transfer effect and improve heat transfer film coefficient, the effect of increasing heat transfer efficiency
- Summary
- Abstract
- Description
- Claims
- Application Information
AI Technical Summary
Problems solved by technology
Method used
Image
Examples
Embodiment 1
[0050] One of the specific implementations of a cast plate air preheater with baffle fins of the present invention, refer to figure 1 with figure 2 shown in figure 1 It includes a housing 2, a flue gas inlet 1, a flue gas outlet 7, an air inlet 6, an air outlet 4, and a heat exchange element 3 and a sealing structure 5 arranged in the housing 2. The heat exchange element 3 includes a plurality of Cast finned plate heat exchange unit, in figure 2 The cast finned plate heat exchange unit includes a base plate 31 and a fin group arranged on the base plate 31. The cast finned plate heat exchange unit is arranged in alignment with two base plates 31, and is sealed and connected through sealing bolts 10 respectively. The sealing surface 32 at its edge end. The heat exchange element 3 is made of casting or alloy. The two base plates 31 of the cast finned plate heat exchange unit are sealed and connected to the sealing surfaces 32 at both ends by sealing bolts 10 to form a cast f...
Embodiment 2
[0059] The second embodiment of a baffle-fin cast plate air preheater of the present invention, as image 3 with Figure 4 As shown, the main technical solutions of this embodiment are the same as those of Embodiment 1, and the features not explained in this embodiment are explained in Embodiment 1, and will not be repeated here. The difference between this embodiment and Embodiment 1 is that in the group of fins that include the baffle-shaped fins 314, the number of bends and the deflection angles of the base of the baffle-shaped fins 314 are set the same, and the baffle-shaped fins The base body of the sheet 314 is bent once to form a flow guide part 3141 and a flow guide part 3142 connected to each other, wherein the flow guide part 3141 is aligned with the direction of the longitudinal airflow channel ( Figure 4 The angle between the A direction) is the diversion angle φ 1. The angle between the diversion part 3142 and the diversion part 3141 is the deflection angle ...
Embodiment 3
[0061] The third specific embodiment of a baffle-fin cast plate air preheater of the present invention, as Figure 5 As shown, the main technical solutions of this embodiment are the same as those of Embodiment 1, and the features not explained in this embodiment are explained in Embodiment 1, and will not be repeated here. The difference between this embodiment and Embodiment 1 is that the fin groups arranged on one side or both sides of the substrate 31 are composed of single-fold manifold fins 315 and straight fins 312 bent once, and the single-fold manifold fins are bent once. The fins 315 and the straight fins 312 can be arranged in rows or mixed respectively.
PUM
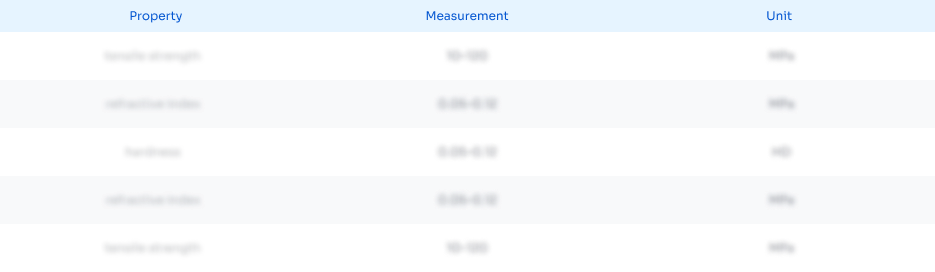
Abstract
Description
Claims
Application Information

- Generate Ideas
- Intellectual Property
- Life Sciences
- Materials
- Tech Scout
- Unparalleled Data Quality
- Higher Quality Content
- 60% Fewer Hallucinations
Browse by: Latest US Patents, China's latest patents, Technical Efficacy Thesaurus, Application Domain, Technology Topic, Popular Technical Reports.
© 2025 PatSnap. All rights reserved.Legal|Privacy policy|Modern Slavery Act Transparency Statement|Sitemap|About US| Contact US: help@patsnap.com