High-strength insulator silica gel and preparation method thereof
An insulator and high-strength technology, applied in the field of rubber material manufacturing, can solve the problem that the strength of silicone rubber is difficult to reach the insulator, and achieve high-strength characteristics and the effect of not being easily deformed
- Summary
- Abstract
- Description
- Claims
- Application Information
AI Technical Summary
Problems solved by technology
Method used
Image
Examples
Embodiment 1
[0013] A high-strength insulator silica gel and a preparation method thereof, the preparation method is as follows; first add 100 parts of methyl vinyl raw rubber with a vinyl molar content of 0.2% in a kneader, and stir for 2-4 minutes; mix 50 parts of white Carbon black, 400 parts of aluminum hydroxide, 2 parts of stearic acid 1801, 4 parts of hydroxy silicone oil and 4 parts of vinyltriethoxysilane were added in several times, and fully stirred after each addition to obtain a silicone rubber mixture; kneading After molding, the temperature is raised to 150°C, cooled to 80°C with cooling water, and the glue is produced to obtain the mixed silicone rubber; after the glue is produced, it is cooled to room temperature to obtain the product.
[0014] Vulcanizing agent can be added to vulcanize during use, vulcanized at 170 degrees Celsius for 5 minutes, and secondary vulcanized at 200 degrees Celsius for 4 hours.
Embodiment 2
[0016] A high-strength insulator silica gel and a preparation method thereof, the preparation method is as follows; first add 100 parts of methyl vinyl raw rubber with a vinyl molar content of 0.2% in a kneader, and stir for 2-4 minutes; mix 60 parts of white Carbon black, 300 parts of aluminum hydroxide, 3 parts of stearic acid 1801, 3 parts of hydroxy silicone oil and 3 parts of vinyltriethoxysilane were added in several times, and fully stirred after each addition to obtain a silicone rubber mixture; kneading After molding, the temperature is raised to 150°C, cooled to 80°C with cooling water, and the glue is produced to obtain the mixed silicone rubber; after the glue is produced, it is cooled to room temperature to obtain the product.
[0017] Vulcanizing agent can be added to vulcanize during use, vulcanized at 170 degrees Celsius for 5 minutes, and secondary vulcanized at 200 degrees Celsius for 4 hours.
Embodiment 3
[0019] A high-strength insulator silica gel and a preparation method thereof, the preparation method is as follows; first add 100 parts of methyl vinyl raw rubber with a vinyl molar content of 0.2% in a kneader, and stir for 2-4 minutes; mix 80 parts of white Carbon black, 200 parts of aluminum hydroxide, 2 parts of stearic acid 1801, 5 parts of hydroxy silicone oil and 5 parts of vinyltriethoxysilane were added in several times, and fully stirred after each addition to obtain a silicone rubber mixture; kneading After molding, the temperature is raised to 150°C, cooled to 80°C with cooling water, and the glue is produced to obtain the mixed silicone rubber; after the glue is produced, it is cooled to room temperature to obtain the product.
[0020] Vulcanizing agent can be added to vulcanize during use, vulcanized at 170 degrees Celsius for 5 minutes, and secondary vulcanized at 200 degrees Celsius for 4 hours.
[0021] To sum up, the silica gel for high-strength insulators of...
PUM
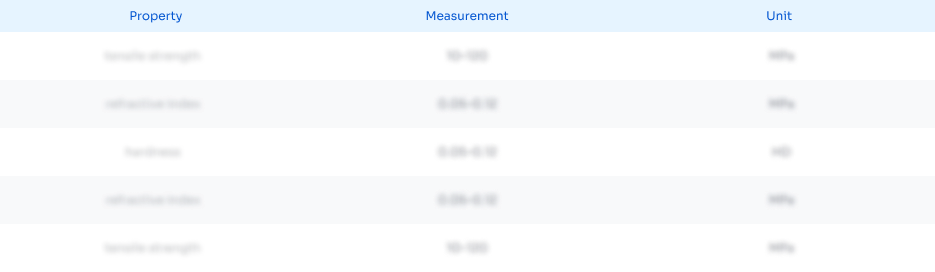
Abstract
Description
Claims
Application Information

- R&D Engineer
- R&D Manager
- IP Professional
- Industry Leading Data Capabilities
- Powerful AI technology
- Patent DNA Extraction
Browse by: Latest US Patents, China's latest patents, Technical Efficacy Thesaurus, Application Domain, Technology Topic, Popular Technical Reports.
© 2024 PatSnap. All rights reserved.Legal|Privacy policy|Modern Slavery Act Transparency Statement|Sitemap|About US| Contact US: help@patsnap.com