Material used for solar cell rear panels and preparation method of material
A technology for solar cells and back sheets, applied in the field of solar cells, can solve the problems of the complexity of the production process, the reduction of efficiency, the increase of production costs, etc., and achieve the effects of excellent water vapor barrier properties, avoiding the use of adhesives, and good performance.
- Summary
- Abstract
- Description
- Claims
- Application Information
AI Technical Summary
Problems solved by technology
Method used
Image
Examples
Embodiment 1
[0020] Add 3-fluoro-1,2-propanediol and 1,4-butanediol with a molar ratio of 1:1 into the reactor with a reflux and stirring device, and then add 2,6-naphthalene dicarboxylic acid with a molar ratio of 0.9:1 and isophthalic acid were added, wherein the ratio of the total moles of diols to the total moles of dibasic acids was controlled at 1.40:1, and the stirrer was started at 60 revolutions per minute; the mixture was heated to 210°C , add 100ppm of tetrabutyl titanate and 20ppm of sodium tungstate relative to the total mass of alcohol and acid, and react for 4 hours under stirring, then add europium carbonate hydrate and graphene oxide with a mass ratio of 0.4:1, and the addition amount is 9% of the total mass of alcohol and acid; increase the stirring speed to 210 rpm, and stir for 30 minutes; then use a vacuum pump to extract the air in the reactor, and use 1.5 hours to make the vacuum of the system greater than 100Pa, and then react at 210°C for 3 hour, promptly obtain th...
Embodiment 2
[0022] Add 3-fluoro-1,2-propanediol and 1,4-butanediol with a molar ratio of 2:1 into the reactor with a reflux and stirring device, and then add 2,6-naphthalene dicarboxylic acid with a molar ratio of 0.4:1 and isophthalic acid are added therein, wherein the ratio of the total moles of dibasic alcohols to the total moles of dibasic acids is controlled at 1.2:1, and the stirrer is started at a speed of 60 revolutions per minute; the mixture is heated to 220°C , add 200ppm of zinc acetate and 30ppm of sodium tungstate relative to the total mass of alcohol and acid, and react for 4 hours under stirring, then add hydrated europium carbonate and graphene oxide with a mass ratio of 0.48:1. 7% of the mass; increase the stirring speed to 210 rpm, and stir for 30 minutes; then use a vacuum pump to extract the air in the reactor, use 2 hours to make the vacuum of the system greater than 100Pa, and then react at 240 ° C for 4 hours to obtain Materials described in the present invention....
Embodiment 3
[0024] Add 3-fluoro-1,2-propanediol and 1,4-butanediol in a molar ratio of 3:1 into a reaction kettle with a reflux and stirring device, and then add 2,6-naphthalene dicarboxylic acid in a molar ratio of 1:1 and isophthalic acid are added therein, wherein the ratio of the total moles of dibasic alcohols to the total moles of dibasic acids is controlled at 1.4:1, and the stirrer is started at a speed of 80 revolutions per minute; the mixture is heated to 210°C , add 200ppm of zinc acetate and 30ppm of sodium tungstate relative to the total mass of alcohol and acid, and react for 4 hours under stirring, then add hydrated europium carbonate and graphene oxide with a mass ratio of 0.6:1. 19% of the mass; increase the stirring speed to 220 rpm, and stir for 30 minutes; then use a vacuum pump to extract the air in the reactor, use 2 hours to make the vacuum of the system greater than 100Pa, and then react at 240 ° C for 5 hours to obtain Materials described in the present invention....
PUM
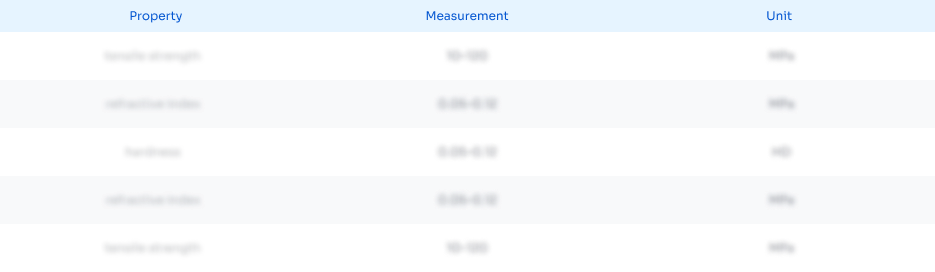
Abstract
Description
Claims
Application Information

- R&D Engineer
- R&D Manager
- IP Professional
- Industry Leading Data Capabilities
- Powerful AI technology
- Patent DNA Extraction
Browse by: Latest US Patents, China's latest patents, Technical Efficacy Thesaurus, Application Domain, Technology Topic, Popular Technical Reports.
© 2024 PatSnap. All rights reserved.Legal|Privacy policy|Modern Slavery Act Transparency Statement|Sitemap|About US| Contact US: help@patsnap.com