Method for recovering gold, silver, tin and copper from industrial wastes
A technology for recovering gold from industrial waste, which is applied in silver, tin, copper, and gold recovery from industrial waste, can solve the problems of unsuitability for long-term and large-scale use, waste of social resources, low recovery efficiency, etc., and achieve investment cost and operating cost Low, economic benefits of energy saving and emission reduction, high recovery rate and enrichment rate
- Summary
- Abstract
- Description
- Claims
- Application Information
AI Technical Summary
Problems solved by technology
Method used
Examples
Embodiment 1
[0040] Take the tin anode slime just out of the tank from the factory (metal content: Au25g / T, Ag2200g / T, Sn46.2%, Cu18.5%), first use a ball mill to grind the anode slime to less than 80 mesh, take 1000g of it and use it to configure A good 5mol / L hydrochloric acid solution 4950mL and hydrogen peroxide 50mL were subjected to oxidative acid leaching treatment, reacted under stirring, the reaction time was 5 hours, the reaction temperature was 90°C, the liquid-solid ratio was 5:1, and the liquid potential after leaching was controlled to 400mv. After the reaction was completed, it was filtered, and the dried weight of the filter residue was 44.7g. After analysis, the contents of each metal were Au561g / T, Ag47300g / T, tin 18.2%, and copper 8.6%. The gold slag rate is close to 100%, and the silver slag rate is 96.1%. Cool the filtrate to room temperature, add 500g of reduced iron powder, stir until the solution no longer discolors the bright tin bars, and filter to obtain sponge c...
Embodiment 2
[0042] Take the tin anode slime just out of the tank from the factory (metal content: Au25g / T, Ag2200g / T, Sn46.2%, Cu18.5%), first use a ball mill to grind the anode slime to less than 80 mesh, take 1000g of it and use 7mol / L regenerated hydrochloric acid solution 4950mL and hydrogen peroxide 50mL were subjected to oxidative acid leaching treatment, reacted under stirring, the reaction time was 3 hours, the reaction temperature was 50°C, the liquid-solid ratio was 5:1, and the liquid potential after leaching was controlled to 450mv. After the reaction was completed, it was filtered, and the dried weight of the filter residue was 108.4g. The analyzed content was Au229g / T, Ag19550g / T, Sn22.3%, Cu9.8%. The gold slag rate is close to 100%, and the silver slag rate is 96.3%. Cool the filtrate to room temperature, add 500g of iron filings, stir until the solution no longer discolors the bright tin bars, and filter to obtain sponge copper. The dry weight of sponge copper is 408.9g, ...
Embodiment 3
[0044] Take 1000g of polishing ash from a factory (the main components are tin-copper alloy and quartz sand, containing 32.6% tin and 8.4% copper), and use a prepared 6mol / L hydrochloric acid solution to carry out oxidative acid leaching treatment on it, and react under stirring. The time is 2 hours, the reaction temperature is 90° C., the liquid-solid ratio is 8:1, the amount of iron trioxide added is 80 g, and the liquid potential after leaching is controlled to be 500 mv. After the reaction was completed, it was filtered, and the dried weight of the filter residue was 534.3g, and the analyzed content was 2.3% Sn and 0.2% Cu. Cool the filtrate to room temperature, add 100g of reduced iron powder, stir until the solution no longer discolors the bright tin bars, and filter to obtain sponge copper. The dry weight of sponge copper is 89.2g, the copper content is 91.2%, and the copper yield is 96.8%. The solution after the copper replacement is adjusted to pH 4 with calcium hydro...
PUM
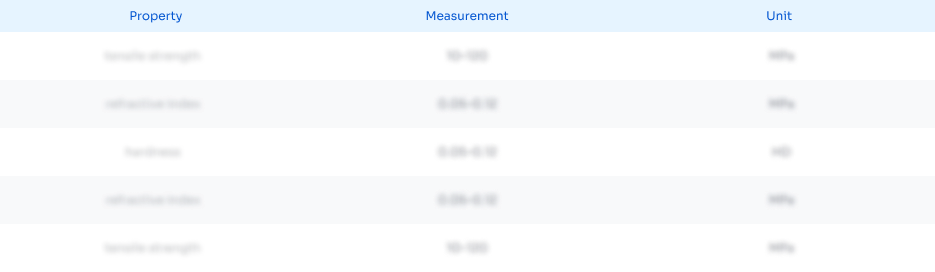
Abstract
Description
Claims
Application Information

- Generate Ideas
- Intellectual Property
- Life Sciences
- Materials
- Tech Scout
- Unparalleled Data Quality
- Higher Quality Content
- 60% Fewer Hallucinations
Browse by: Latest US Patents, China's latest patents, Technical Efficacy Thesaurus, Application Domain, Technology Topic, Popular Technical Reports.
© 2025 PatSnap. All rights reserved.Legal|Privacy policy|Modern Slavery Act Transparency Statement|Sitemap|About US| Contact US: help@patsnap.com