Manufacturing method of GH3600 nickel alloy extruded tube
A nickel alloy, extrusion tube technology, applied in metal extrusion control equipment, metal extrusion, metal extrusion dies, etc., can solve the problems of increased processing procedures, excessively long processing process, and poor quality of extruded pipe materials. Achieve the effect of preventing the generation of surface oxide layers and defects, reducing heating temperature and heating time, and reducing the probability of contact
- Summary
- Abstract
- Description
- Claims
- Application Information
AI Technical Summary
Problems solved by technology
Method used
Image
Examples
Embodiment 1
[0034] combine figure 1 , figure 2 with image 3 , the preparation method of the present embodiment GH3600 nickel alloy extruded pipe comprises the following steps:
[0035] Step 1. Machining the GH3600 nickel alloy ingot to obtain an extruded billet 1; the cross-sectional shape of the extruded billet 1 is a circular ring with an inner diameter of 24 mm and an outer diameter of 81 mm;
[0036] Step 2. When the degree of vacuum is not greater than 1×10 -1 In the vacuum welding box of Pa, the inner and outer surfaces of the extruded billet 1 described in step 1 are clad with copper tubes 2, and the cladding thickness of the inner surface of the extruded billet 1 is the same as that of the outer surface of the extruded billet 1. The cladding thickness on the surface is 1 mm, and the cladding ingot 3 is obtained; the cross-sectional shape of the cladding ingot 3 is a circular ring with an inner diameter of 22 mm and an outer diameter of 83 mm;
[0037] Step 3: heat the clad bil...
Embodiment 2
[0045] combine figure 1 with figure 2 , the preparation method of the present embodiment GH3600 nickel alloy extruded pipe comprises the following steps:
[0046] Step 1. Machining the GH3600 nickel alloy ingot to obtain an extruded billet 1; the cross-sectional shape of the extruded billet 1 is a circular ring with an inner diameter of 24 mm and an outer diameter of 79 mm;
[0047] Step 2. When the degree of vacuum is not greater than 1×10 -1 In the vacuum welding box of Pa, the inner and outer surfaces of the extruded billet 1 described in step 1 are clad with copper tubes 2, and the cladding thickness of the inner surface of the extruded billet 1 is the same as that of the outer surface of the extruded billet 1. The cladding thickness on the surface is 2mm, and the cladding ingot 3 is obtained; the cross-sectional shape of the cladding ingot 3 is a circular ring with an inner diameter of 20mm and an outer diameter of 83mm;
[0048] Step 3: heat the clad ingot 3 describe...
Embodiment 3
[0056] combine figure 1 with figure 2 , the preparation method of the present embodiment GH3600 nickel alloy extruded pipe comprises the following steps:
[0057] Step 1. Machining the GH3600 nickel alloy ingot to obtain an extruded billet 1; the cross-sectional shape of the extruded billet 1 is a circular ring with an inner diameter of 26 mm and an outer diameter of 81 mm;
[0058] Step 2. When the degree of vacuum is not greater than 1×10 -1 In the vacuum welding box of Pa, the inner and outer surfaces of the extruded billet 1 described in step 1 are clad with copper tubes 2, and the cladding thickness of the inner surface of the extruded billet 1 is the same as that of the outer surface of the extruded billet 1. The cladding thickness on the surface is 1.5 mm, and the cladding ingot 3 is obtained; the cross-sectional shape of the cladding ingot 3 is a circular ring with an inner diameter of 23 mm and an outer diameter of 84 mm;
[0059] Step 3: heat the clad billet 3 de...
PUM
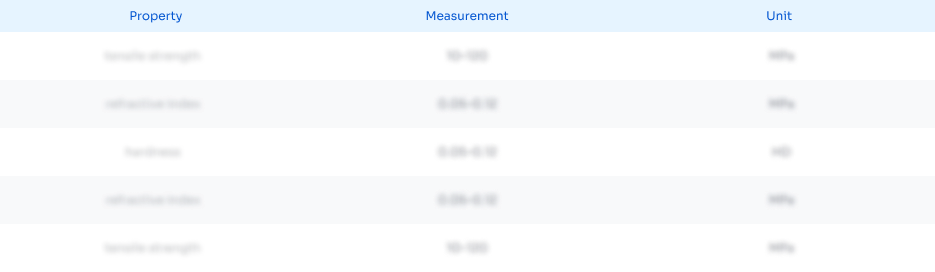
Abstract
Description
Claims
Application Information

- Generate Ideas
- Intellectual Property
- Life Sciences
- Materials
- Tech Scout
- Unparalleled Data Quality
- Higher Quality Content
- 60% Fewer Hallucinations
Browse by: Latest US Patents, China's latest patents, Technical Efficacy Thesaurus, Application Domain, Technology Topic, Popular Technical Reports.
© 2025 PatSnap. All rights reserved.Legal|Privacy policy|Modern Slavery Act Transparency Statement|Sitemap|About US| Contact US: help@patsnap.com