Epoxy resin and polyurethane composite heat transfer printing adhesive and preparation method thereof
A technology of epoxy resin and polyurethane, used in epoxy resin glue, polyurea/polyurethane adhesive, adhesive and other directions, can solve the problem of unsatisfactory properties such as scratch resistance, adhesion, water resistance and high temperature resistance of transfer patterns and other problems, to achieve the effect of improving oxidation resistance, corrosion resistance and weather resistance
- Summary
- Abstract
- Description
- Claims
- Application Information
AI Technical Summary
Problems solved by technology
Method used
Examples
Embodiment Construction
[0010] A composite thermal transfer adhesive of epoxy resin and polyurethane, made of the following raw materials in parts by weight (kg): polyurethane resin (KL-540E) 25, E-12 epoxy resin 10, sorbitan fatty acid ester 12 , polyglycerin fatty acid ester 5, epoxidized triglyceride 3, epoxy tetrahydrophthalate dioctyl 3, silane coupling agent KH550 5, ethylene glycol 6, tert-butyl peroxybenzoate 3 , Alkylphenol polyoxyethylene ether 8, antioxidant DLTP1, antioxidant DSTP3, 1-hydroxyethyl-2-oleyl imidazoline 2, HDI trimer 2, propylenediamine 1, acetone 35, xylene 65.
[0011] Include the following steps:
[0012] (1) Put sorbitan fatty acid ester and polyglycerol fatty acid ester into acetone, heat to 70-80°C, then add cumene hydroperoxide, silane coupling agent KH550, ethylene glycol , stirred and reacted for 40-50 minutes, heated to 110-120°C, added epoxy tetrahydrophthalate dioctyl, antioxidant DSTP, 1-hydroxyethyl-2-oleyl imidazoline, stirred and reacted 2- 3 hours;
[00...
PUM
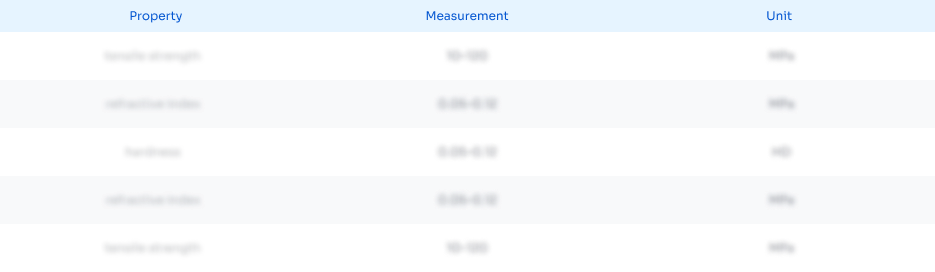
Abstract
Description
Claims
Application Information

- R&D
- Intellectual Property
- Life Sciences
- Materials
- Tech Scout
- Unparalleled Data Quality
- Higher Quality Content
- 60% Fewer Hallucinations
Browse by: Latest US Patents, China's latest patents, Technical Efficacy Thesaurus, Application Domain, Technology Topic, Popular Technical Reports.
© 2025 PatSnap. All rights reserved.Legal|Privacy policy|Modern Slavery Act Transparency Statement|Sitemap|About US| Contact US: help@patsnap.com