Welding method adaptable to high-temperature sputtering target material
A welding method, high-temperature sputtering technology, which is applied in the field of new material welding, and can solve problems such as not being able to withstand high temperatures
- Summary
- Abstract
- Description
- Claims
- Application Information
AI Technical Summary
Problems solved by technology
Method used
Examples
Embodiment Construction
[0012] A welding method suitable for high-temperature sputtering targets, characterized in that it comprises the following steps:
[0013] (1) Clean the welding surface of the target and the back plate;
[0014] (2) Add silver powder with a weight percentage of 60%-70% or activated carbon particles with a weight percentage of 70%-80% to the epoxy resin glue, and evenly coat the welding surface of the target and the back plate and both sides of the copper mesh;
[0015] (3) Place the copper mesh and the target on the backplane in turn and position them;
[0016] (4) Place a certain weight of briquettes on the target;
[0017] (5) Curing under normal temperature and pressure environment;
[0018] (6) After cooling, remove excess glue on the edge of the target.
[0019] The silicon target welded by this method was provided to a touch screen manufacturer, and the sputtering efficiency of the customer increased by 15-20%, which improved the production efficiency. However, the ta...
PUM
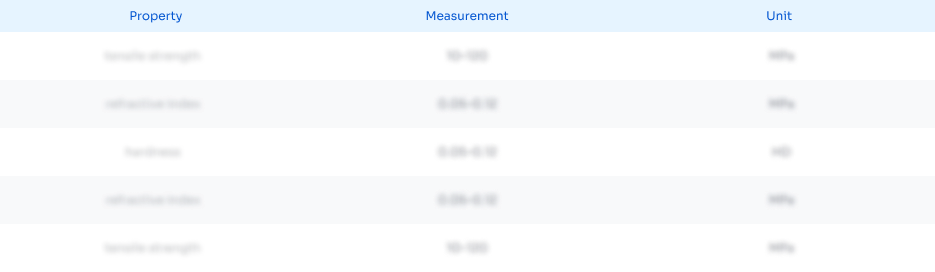
Abstract
Description
Claims
Application Information

- R&D
- Intellectual Property
- Life Sciences
- Materials
- Tech Scout
- Unparalleled Data Quality
- Higher Quality Content
- 60% Fewer Hallucinations
Browse by: Latest US Patents, China's latest patents, Technical Efficacy Thesaurus, Application Domain, Technology Topic, Popular Technical Reports.
© 2025 PatSnap. All rights reserved.Legal|Privacy policy|Modern Slavery Act Transparency Statement|Sitemap|About US| Contact US: help@patsnap.com