Method for plating copper on stainless steel
A technology of stainless steel and copper plating, which is applied in the field of electrochemistry, can solve problems such as environmental pollution and reduce production costs, and achieve the effects of reducing environmental pollution, reducing industrial processes, and reducing corrosion
- Summary
- Abstract
- Description
- Claims
- Application Information
AI Technical Summary
Problems solved by technology
Method used
Examples
Embodiment 1
[0023] The formula of the pre-plating solution containing iron, nickel and chromium metal cations is: 110g / L CrCl 3 ·6H 2 O, 45g / L NiCl 2 ·6H 2 O, 30g / L FeCl 2 ·4H 2 O, 15g / L NaCl, 30g / L NH 4 Cl, 20g / L H 3 BO 3 , 20g / L Glycine.
[0024] The formula of acid sulfate bath: 180g / L CuSO 4 ·5H 2 O, 60g / L H 2 SO 4 , 0.06g / L Cl - .
[0025] The process is as follows: Take a stainless steel plate with a length of 10cm, a width of 5cm, and a thickness of 3mm, and one side of the stainless steel plate is insulated. Under the conditions of a treatment time of 2min and a temperature of 55℃, use the 2 CO 3 , 15g / L Na 3 PO 4 ·12H 2 O, 8g / L JT-100 (maleic anhydride acrylic copolymer) solution is thoroughly degreasing, washed with distilled water, placed on the conductive cathode plate in the electrolytic tank of the pre-plating solution, and the metal corresponding to the pre-plating solution The plate is the anode, and the cathode current density is 1A / dm2, the temperature is 25℃, the frequency i...
Embodiment 2
[0027] The formula of the pre-plating solution containing iron, nickel and chromium metal cations is: 100g / L CrCl 3 ·6H 2 O, 30g / L NiSO 4 , 20g / L FeSO 4 , 5g / L Na 2 SO 4 , 30g / L NH 4 Cl, 25g / L NaCl, 20g / L H 3 BO 3 , 15g / L thiourea.
[0028] The formula of acid sulfate bath: 170g / L CuSO 4 ·5H 2 O, 70g / L H 2 SO 4 , 0.06g / L Cl - .
[0029] The process is as follows: Take a stainless steel plate with a length of 25cm, a width of 40cm, and a thickness of 2mm. One side of the stainless steel plate is insulated. Under the conditions of a treatment time of 2min and a temperature of 60℃, use 10g / L NaOH, 20g / L Na 2 CO 3 , 15g / L Na 3 PO 4 ·12H 2 O, 8g / L JT-100 (maleic anhydride acrylic copolymer) solution is thoroughly degreasing, washed with distilled water, placed on the conductive cathode plate in the electrolytic tank of the pre-plating solution, and the metal corresponding to the pre-plating solution The plate is the anode, and the cathode current density is 2A / dm2, the temperature is...
Embodiment 3
[0031] The formula of the pre-plating solution containing iron, nickel and chromium metal cations: 130g / L CrCl 3 ·6H 2 O, 40g / L NiCl 2 ·6H 2 O, 20g / L FeCl 2 ·4H 2 O, 5g / L NaCl, 30g / L NH 4 Cl, 20g / L H 3 BO 3 , 30g / L 5-sulfosalicylic acid.
[0032] The formula of acid sulfate bath: 180g / L CuSO 4 ·5H 2 O, 60g / L H 2 SO 4 , 0.06g / L Cl - .
[0033] The process is as follows: take a stainless steel plate with a length of 25cm, a width of 40cm, and a thickness of 2mm, and one side of the stainless steel plate is insulated. Under the conditions of a treatment time of 2min and a temperature of 60℃, use 10g / L NaOH, 20g / L Na 2 CO 3 , 15g / L Na 3 PO 4 ·12H 2 O, 8g / L JT-100 (maleic anhydride acrylic copolymer) solution is completely degreasing, washed with distilled water, and placed on the conductive cathode plate in the electrolytic tank of the pre-plating solution, with the metal corresponding to the pre-plating solution The plate is the anode. Under the conditions of cathode current densi...
PUM
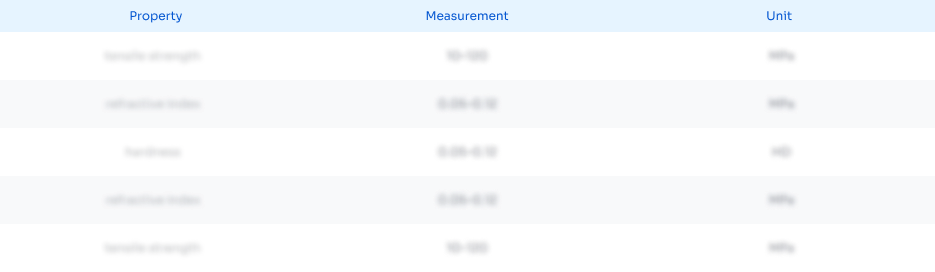
Abstract
Description
Claims
Application Information

- R&D
- Intellectual Property
- Life Sciences
- Materials
- Tech Scout
- Unparalleled Data Quality
- Higher Quality Content
- 60% Fewer Hallucinations
Browse by: Latest US Patents, China's latest patents, Technical Efficacy Thesaurus, Application Domain, Technology Topic, Popular Technical Reports.
© 2025 PatSnap. All rights reserved.Legal|Privacy policy|Modern Slavery Act Transparency Statement|Sitemap|About US| Contact US: help@patsnap.com