Production method of vanadium-nitrogen alloy
A technology of vanadium nitrogen alloy and production method, which is applied in the field of metallurgy, can solve the problems of vanadium trioxide being unstable in normal state, demanding temperature control, and low melting point of vanadium pentoxide, etc., and achieves low production cost, low temperature control requirements, The effect of stable production process
- Summary
- Abstract
- Description
- Claims
- Application Information
AI Technical Summary
Problems solved by technology
Method used
Examples
Embodiment 1
[0027] In the tunnel kiln, the mixed gas of nitrogen and hydrogen is continuously fed, the pressure of nitrogen and hydrogen is 0.5MPa, and the flow rate of nitrogen is 4m 3 / h, hydrogen flow rate is 6.5m 3 / h, put 1000kg of vanadium pentoxide into the tunnel kiln and reduce it to 912kg of vanadium tetroxide. The temperature of the tunnel kiln is 400°C, and the holding time is 4 hours; The dry powder pressing ball is carried out on the machine, the feeding speed of the rolling ball machine is 3000kg / h, the forming pressure of the rolling ball machine is 80Mpa, and the ellipsoid billet with a diameter of 30mm and a thickness of 10mm is produced, and the formed billet is put into the intermediate frequency vertical In the furnace, vacuumize the intermediate frequency furnace to 280pa, heat it to 1000°C at the same time, and keep it warm for 2 hours; fill the furnace with nitrogen to ensure a positive pressure of 0.8Mpa, raise the temperature to 1400°C in a nitrogen environment, ...
Embodiment 2
[0030] In the tunnel kiln, the mixed gas of nitrogen and hydrogen is continuously fed, the pressure of nitrogen and hydrogen is 0.5MPa, and the flow rate of nitrogen is 4.5m 3 / h, hydrogen flow rate is 7m 3 / h, put 1000kg of vanadium pentoxide into the tunnel kiln and reduce it to 912kg of vanadium tetroxide. The temperature of the tunnel kiln is 450°C, and the holding time is 4 hours; The dry powder pressing ball is carried out on the machine, the feeding speed of the rolling ball machine is 3000kg / h, the forming pressure of the rolling ball machine is 60Mpa, the formed billet is put into the intermediate frequency shaft furnace, and the intermediate frequency furnace is vacuumed to 280pa, At the same time, heat to 1000°C and keep it warm for 2 hours; fill the furnace with nitrogen to ensure a positive pressure of 0.8Mpa, raise the temperature to 1200-1500°C in a nitrogen environment, and keep it warm for 4 hours. This process mainly occurs carbonization reaction to generate ...
PUM
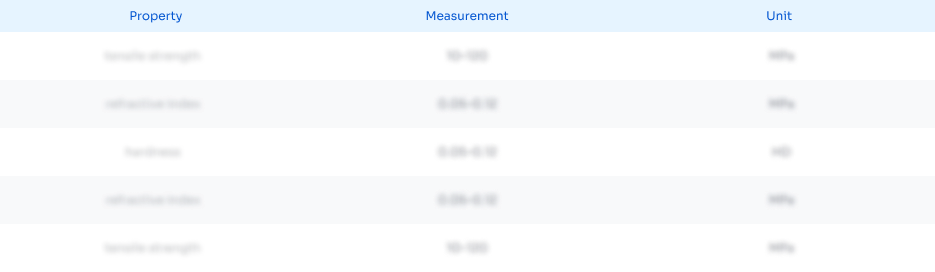
Abstract
Description
Claims
Application Information

- R&D
- Intellectual Property
- Life Sciences
- Materials
- Tech Scout
- Unparalleled Data Quality
- Higher Quality Content
- 60% Fewer Hallucinations
Browse by: Latest US Patents, China's latest patents, Technical Efficacy Thesaurus, Application Domain, Technology Topic, Popular Technical Reports.
© 2025 PatSnap. All rights reserved.Legal|Privacy policy|Modern Slavery Act Transparency Statement|Sitemap|About US| Contact US: help@patsnap.com