High-temperature alloy turbine blade repair material and repair process using same
A technology of turbine blades and superalloys, applied in metal processing equipment, manufacturing tools, arc welding equipment, etc., can solve problems such as surface damage
- Summary
- Abstract
- Description
- Claims
- Application Information
AI Technical Summary
Problems solved by technology
Method used
Image
Examples
Embodiment 1
[0029] In this example, the micro-arc spark deposition repair material is composed of the following components by weight percentage: Co15%, Cr18%, Al6.5%, Ta4%, Re2%, Y0.56%, C0.04%, and the rest is Ni . The above-mentioned repair material is made into a round bar with a diameter of 3mm and a length of 50mm, and the area to be repaired is surfacing by using the micro-arc spark deposition process. The surfacing welding process parameters are 800W power and 300HZ frequency. After the processing is completed, the repaired parts are put into a vacuum furnace for heat treatment. The heat treatment system: first solid solution at 1200°C for 3 hours, air-cooled to room temperature; then aged at 850°C for 10 hours, and cooled to room temperature with the furnace.
[0030] As shown in Figure 1(a)-(b), it can be seen that there is no crack in the repair layer, the bonding interface between the repair layer and the blade matrix is metallurgical fusion, the structure is uniform, and the...
Embodiment 2
[0032] In this embodiment, the micro-arc spark deposition repair material is composed of the following components by weight percentage: Co18%, Cr10%, Al7%, Ta8%, Re2%, Hf0.24%, Y0.75%, C0.01%, The rest is Ni. The above-mentioned repair material is made into a round bar with a diameter of 6mm and a length of 100mm, and the micro-arc spark deposition process is used to perform surfacing welding on the area to be repaired. The surfacing welding process parameters are power 200W, frequency 150HZ, and the processing process is carried out in a vacuum glove box. After the processing is completed, the repaired parts are put into a vacuum furnace for heat treatment. The heat treatment system: first solid solution at 1150°C for 4 hours, then air-cooled to room temperature; then aged at 900°C for 4 hours, and cooled to room temperature with the furnace.
[0033] As shown in Figure 2(a)-(b), it can be seen that there is no crack in the repair layer, the bonding interface between the repa...
Embodiment 3
[0035] In this embodiment, the micro-arc spark deposition repair material is composed of the following components by weight percentage: Co5%, Cr20%, Al5%, Ta2%, Re5%, Hf2%, Y0.9%, C0.1%, and the rest are Ni. The above-mentioned repair material is made into a round bar with a diameter of 2mm and a length of 30mm, and the area to be repaired is surfacing by using the micro-arc spark deposition process. It is carried out in the box. After the processing is completed, the repaired parts are put into a vacuum furnace for heat treatment. The heat treatment system: first solid solution at 1230°C for 2 hours, then air-cooled to room temperature; then aged at 800°C for 20 hours, and cooled to room temperature with the furnace.
[0036] In this embodiment, the repair layer has no cracks, the bonding interface between the repair layer and the blade matrix is metallurgical fusion, the structure is uniform, and the main strengthening phase is γ'.
PUM
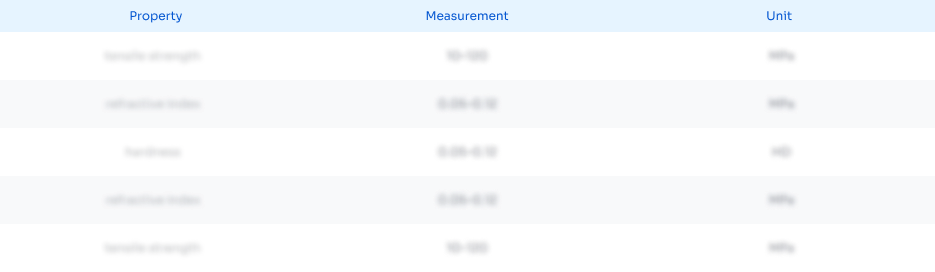
Abstract
Description
Claims
Application Information

- R&D
- Intellectual Property
- Life Sciences
- Materials
- Tech Scout
- Unparalleled Data Quality
- Higher Quality Content
- 60% Fewer Hallucinations
Browse by: Latest US Patents, China's latest patents, Technical Efficacy Thesaurus, Application Domain, Technology Topic, Popular Technical Reports.
© 2025 PatSnap. All rights reserved.Legal|Privacy policy|Modern Slavery Act Transparency Statement|Sitemap|About US| Contact US: help@patsnap.com