Injection mould with rapidly-replaced mould cores
An injection mold and mold core technology, applied in the field of molds, can solve problems such as the influence of replacement efficiency, low tensile strength, and high labor intensity of operators, so as to reduce the requirements of operating proficiency, reduce physical requirements, and improve mold replacement efficiency. Effect
- Summary
- Abstract
- Description
- Claims
- Application Information
AI Technical Summary
Problems solved by technology
Method used
Image
Examples
Embodiment 1
[0055] Such as Figure 1-12 , Shown in 19, is a kind of injection mold that can replace mold core quickly of the present invention, in the present embodiment, is to make test standard spline, seeFigure 9 , the injection mold is composed of a movable mold and a fixed mold, wherein the movable mold and the fixed mold include molding parts, a push-out mechanism, a mold guide part and a pouring system, and the main body of the movable mold is mounted on the movable mold holder 22 by a movable mold holder 22 The movable mold core 12 is composed of the fixed mold body, and the fixed mold body is composed of the fixed mold frame 21 and the fixed mold core 11 movably installed on the fixed mold frame 21. The movable mold frame 22 and the fixed mold frame 21 are collectively referred to as the mold frame, and the movable mold core 12 The mold core and the fixed mold core 11 are collectively referred to as the mold core. The mold core is a movable molding part separated from the mold fra...
Embodiment 2
[0076] Such as Figures 13 to 18 As shown, the difference between this embodiment and embodiment 1 is: the injection mold cavity on the mold core is different, see Figure 15 , the injection molded part suitable for the mold core of this embodiment is a cantilever beam 91, a bending standard test sample 92, and an impact standard test sample 93, and two movable inserts 70, 71 are arranged on the clamping surface of the fixed mold core 11, The movable inserts are centered on the pouring hole (that is, the inner channel 54 of the sprue bushing) and are distributed front and rear. There are two mold cavities 73 on the mold clamping surface of the movable mold core 12. The two mold cavities on the movable mold core are connected with the The movable inserts 70 and 71 correspond to each other. When the mold is closed, the movable inserts are located in the mold cavity of the movable mold core to form 4 injection molding chambers for injection molding a single injection molded part,...
PUM
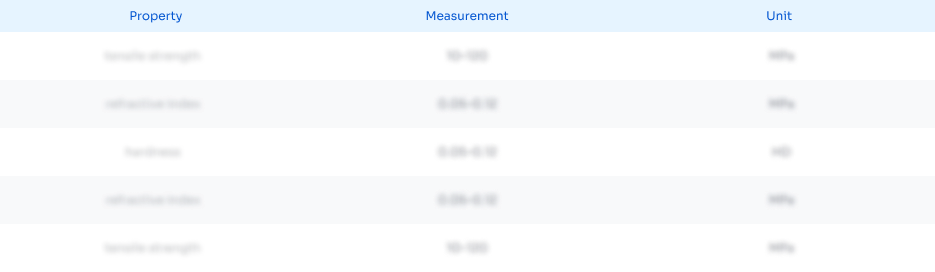
Abstract
Description
Claims
Application Information

- R&D
- Intellectual Property
- Life Sciences
- Materials
- Tech Scout
- Unparalleled Data Quality
- Higher Quality Content
- 60% Fewer Hallucinations
Browse by: Latest US Patents, China's latest patents, Technical Efficacy Thesaurus, Application Domain, Technology Topic, Popular Technical Reports.
© 2025 PatSnap. All rights reserved.Legal|Privacy policy|Modern Slavery Act Transparency Statement|Sitemap|About US| Contact US: help@patsnap.com