Non-asbestos composite fiber and preparation method thereof
A composite fiber and asbestos-free technology, applied in chemical instruments and methods, other chemical processes, etc., can solve the problems of low yield of friction materials, low content of slag balls, high content of slag balls, etc., and achieve good thermal stability and low content , good overall performance
- Summary
- Abstract
- Description
- Claims
- Application Information
AI Technical Summary
Problems solved by technology
Method used
Image
Examples
Embodiment Construction
[0022] Below in conjunction with specific embodiment the present invention is described in further detail:
[0023] The weight of each raw material is:
[0024] 1. Fiber material: 200kg
[0025] Rock wool fiber 80kg; mineral wool fiber 60kg; synthetic fiber 60kg.
[0026] 2. Powder material: 80kg
[0027] Talc powder 32kg; bentonite 24kg; vermiculite powder 16kg; kaolin powder 8kg.
[0028] 3. Modified material: 10kg
[0029] 10kg of polymer resin (solution concentration≤50%).
[0030] The preparation method and steps are:
[0031] Mix 80kg of rock wool fiber, 60kg of mineral wool fiber, and 60kg of synthetic fiber, and open the fiber into a fluffy shape with an opener; then mix 32kg of talcum powder, 24kg of bentonite, and 16kg of vermiculite with a particle size of 100 mesh and a 100% pass rate. Stone powder and 8 kg of kaolin powder are surface-activated with 10 kg of polymer resin; finally, the fluffy short fibers and activated powder materials are pulverized and act...
PUM
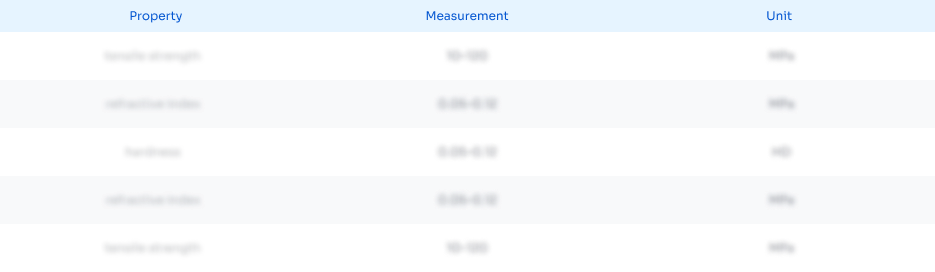
Abstract
Description
Claims
Application Information

- Generate Ideas
- Intellectual Property
- Life Sciences
- Materials
- Tech Scout
- Unparalleled Data Quality
- Higher Quality Content
- 60% Fewer Hallucinations
Browse by: Latest US Patents, China's latest patents, Technical Efficacy Thesaurus, Application Domain, Technology Topic, Popular Technical Reports.
© 2025 PatSnap. All rights reserved.Legal|Privacy policy|Modern Slavery Act Transparency Statement|Sitemap|About US| Contact US: help@patsnap.com