Anti-corrosion FeNiCo magnetically soft alloy with high magnetic induction intensity
A technology of magnetic induction and soft magnetic alloys, applied in the direction of magnetic materials, magnetic objects, electrical components, etc., can solve the problems that cannot fully meet the requirements of device miniaturization, fast response, low sensitivity of electromagnetic devices, poor processing and manufacturing performance, etc. , to achieve the effect of improving anti-corrosion properties, benefiting magnetization, and good magnetic permeability
- Summary
- Abstract
- Description
- Claims
- Application Information
AI Technical Summary
Problems solved by technology
Method used
Image
Examples
Embodiment 1
[0028] The alloy composition (mass percentage) is C: 0.01%, Si: 0.74%, Mn: 0.18%, Ni: 31.99%, Co: 29.12%, Mo: 3.0%, Cu: 0.2%, Ce: 0.02, and the rest is Fe. After smelting and pouring in a vacuum induction furnace, the alloy is heat-preserved at 1200°C, and then hot-forged into a 40mm×200mm slab; After the strip blank is cold-rolled to 2.0mm, it is softened by an intermediate annealing at 1050°C and then cold-rolled into a 0.5mm thick strip. After the cold-rolled strip is heat-treated, the relevant properties are tested. The heat treatment process adopted is: 1180°C×5h, cooled to 700°C at a cooling rate of 150°C / h and quickly cooled to room temperature. 2 Protect. The obtained performance is shown in Table 4:
[0029] Table 4
[0030]
[0031] After vibrating at an acceleration of 3g, the change rate of coercive force Hc of the alloy is 2.56%.
[0032] 50 hours salt spray corrosion corrosion rate is 0.0198mm / a
Embodiment 2
[0034] Alloy composition (mass percentage) is C: 0.01%, Si: 0.50%, Mn: 0.15%, Ni: 30.70%, Co: 30.23%, Mo: 4.0%, Cu: 0.3%, La: 0.01%, Re: 0.01 %, the rest is Fe. After smelting and pouring in a vacuum induction furnace, the alloy is kept at 1220°C, and then hot forged into a 40mm×200mm slab; After the strip blank is cold-rolled to 2.2mm, it is softened by intermediate annealing at 1000°C and then cold-rolled into a 0.5mm thick strip. The cold-rolled strips were subjected to vacuum heat treatment to test related properties. The heat treatment process adopted was: 1150°C×6h, cooled at a cooling rate of 200°C / h to 650°C and quickly cooled to room temperature. The obtained performance is shown in Table 5:
[0035] table 5
[0036]
[0037] After vibrating at an acceleration of 10g, the change rate of the coercive force Hc of the alloy is 2.62%.
[0038] 50 hours salt spray corrosion corrosion rate is 0.0163mm / a
Embodiment 3
[0040] Alloy composition (mass percentage) is C: 0.01%, Si: 0.70%, Mn: 0.13%, Ni: 34.23%, Co: 26.26%, Mo: 3.10%, Cu: 0.32, Ce: 0.01%, Re: 0.01% , and the rest is Fe. After smelting and pouring in a vacuum induction furnace, the alloy is kept at 1150°C and forged into a Ф55mm forging rod with a fast forging machine. After the forged rod is heat-treated, the relevant properties are tested. The heat treatment process adopted is: 1000°C×8h, cooled at a cooling rate of 50°C / h to 700°C and quickly cooled to room temperature. 2 Protect. The obtained performance is shown in Table 6:
[0041] Table 6
[0042]
[0043] After vibrating at an acceleration of 20g, the change rate of the coercive force Hc of the alloy is 2.65%.
[0044] The 50-hour salt spray corrosion corrosion rate is 0.0189mm / a.
PUM
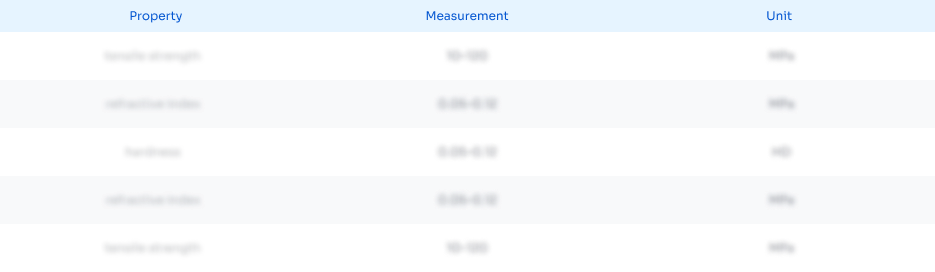
Abstract
Description
Claims
Application Information

- R&D
- Intellectual Property
- Life Sciences
- Materials
- Tech Scout
- Unparalleled Data Quality
- Higher Quality Content
- 60% Fewer Hallucinations
Browse by: Latest US Patents, China's latest patents, Technical Efficacy Thesaurus, Application Domain, Technology Topic, Popular Technical Reports.
© 2025 PatSnap. All rights reserved.Legal|Privacy policy|Modern Slavery Act Transparency Statement|Sitemap|About US| Contact US: help@patsnap.com