A kind of preparation method of lithium battery bamboo charcoal/lithium stannate composite negative electrode material
A negative electrode material, lithium stannate technology, used in battery electrodes, circuits, electrical components, etc., can solve the problems of reducing electrode cycle life, irreversible capacity increase, structure collapse, etc., to avoid excessive capacity decay and slow capacity. Attenuate and suppress the effect of agglomeration
- Summary
- Abstract
- Description
- Claims
- Application Information
AI Technical Summary
Problems solved by technology
Method used
Image
Examples
Embodiment 1
[0021] (1) SnCl with a molar ratio of 0.5:3:2 4 ·5H 2 O: Ethylene glycol: Dissolve citric acid in deionized water, stir at 60°C for 1 hour;
[0022] (2) Then combine with SnCl 4 ·5H 2 O equimolar amount of Li 2 CO 3 Add it and stir at 90°C to evaporate a large amount of water to form a sol;
[0023] (3) Immerse 0.01mol of bamboo charcoal in the sol, so that the sol is completely immersed in the bamboo charcoal. After 1 hour, take out the bamboo charcoal and put it in a drying oven for drying at 180°C; repeat this step 3-4 times;
[0024] (4) Put the bamboo charcoal-xerogel precursor obtained in step (3) into a muffle furnace for rapid sintering to remove excess organic matter, then transfer it to a tube furnace for pre-sintering at 400°C under an argon atmosphere 5h, followed by calcination at 700°C for 4h to obtain bamboo charcoal / lithium stannate composite material.
[0025] The product in Example 1 was assembled into a CR2016 button battery, with a lithium sheet (Φ=1...
Embodiment 2
[0028] (1) SnCl with a molar ratio of 0.5:3:2 4 ·5H 2 O: Ethylene glycol: Dissolve citric acid in deionized water, stir at 60°C for 1 hour;
[0029] (2) Then combine with SnCl 4 ·5H 2 O equimolar amount of Li 2 CO 3 Add it and stir at 90°C to evaporate a large amount of water to form a sol;
[0030] (3) Immerse 0.03mol of bamboo charcoal in the sol, so that the sol is completely submerged in the bamboo charcoal. After 1 hour, take out the bamboo charcoal and put it in a drying oven for drying at 180°C; repeat this step 3-4 times;
[0031] (4) Put the bamboo charcoal-xerogel precursor obtained in step (3) into a muffle furnace for rapid sintering to remove excess organic matter, then transfer it to a tube furnace for pre-sintering at 400°C under an argon atmosphere 5h, followed by calcination at 700°C for 4h to obtain bamboo charcoal / lithium stannate composite material.
[0032]The product in Example 2 was assembled into a CR2016 button battery (the method is the same as...
Embodiment 3
[0033] Embodiment three: (bamboo charcoal amount is different)
[0034] (1) SnCl with a molar ratio of 0.5:3:2 4 ·5H 2 O: Ethylene glycol: Dissolve citric acid in deionized water, stir at 60°C for 1 hour;
[0035] (2) Then combine with SnCl 4 ·5H 2 O equimolar amount of Li 2 CO 3 Add it and stir at 90°C to evaporate a large amount of water to form a sol;
[0036] (3) Immerse 0.025mol of bamboo charcoal in the sol, so that the sol is completely immersed in the bamboo charcoal. After 1 hour, take out the bamboo charcoal and put it in a drying oven for drying at 180°C; repeat this step 3-4 times;
[0037] (4) Put the bamboo charcoal-xerogel precursor obtained in step (3) into a muffle furnace for rapid sintering to remove excess organic matter, then transfer it to a tube furnace for pre-sintering at 400°C under an argon atmosphere 5h, followed by calcination at 700°C for 4h to obtain bamboo charcoal / lithium stannate composite material.
[0038] The product in Example 3 wa...
PUM
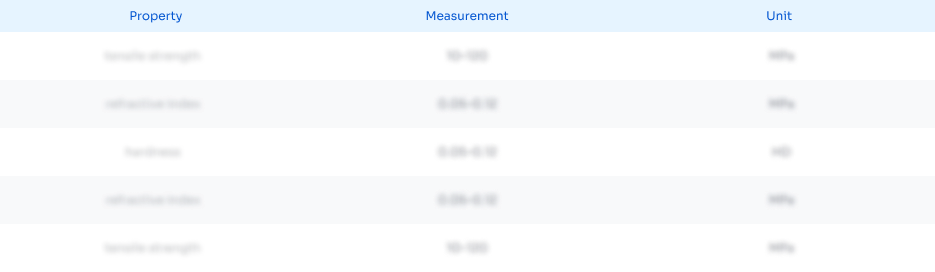
Abstract
Description
Claims
Application Information

- Generate Ideas
- Intellectual Property
- Life Sciences
- Materials
- Tech Scout
- Unparalleled Data Quality
- Higher Quality Content
- 60% Fewer Hallucinations
Browse by: Latest US Patents, China's latest patents, Technical Efficacy Thesaurus, Application Domain, Technology Topic, Popular Technical Reports.
© 2025 PatSnap. All rights reserved.Legal|Privacy policy|Modern Slavery Act Transparency Statement|Sitemap|About US| Contact US: help@patsnap.com