Point welding technique of magnesium alloy filled with reactive powder
A technology of active powder and process method, applied in metal processing equipment, manufacturing tools, welding equipment and other directions, can solve the problems of high equipment and maintenance and operating costs, coarse magnesium alloy grains, and high energy consumption, and achieve ideal engineering practicality. Significance, improved weldability, the effect of flexible formulation
- Summary
- Abstract
- Description
- Claims
- Application Information
AI Technical Summary
Problems solved by technology
Method used
Image
Examples
Embodiment approach 1
[0029] Embodiment 1: The clamping of the materials to be welded is as follows figure 1 As shown, it is a single pulse current welding process. Thermal compensation block 2 is No. 45 steel with a thickness of 1mm. The AZ31 magnesium alloy workpiece 3 is the overlapping joint of two flat plates with a thickness of 0.8mm. Mix 38 parts of active powder 50-mesh titanium dioxide, 42 parts of 50-mesh silicon dioxide, and the rest 50-mesh calcium fluoride medium with alcohol, and then evenly spray it on the surface of the magnesium alloy workpiece 3 to be welded by a pressure sprayer to form a powder Dielectric fill layer 4. The main welding parameters are set as follows: welding current I = 4000A, electrode pressure = 1860N, welding current duration t2 = 1.3s. After the acetone in the powder filling layer is volatilized, the flat plate workpieces to be welded are overlapped and clamped between the upper and lower electrodes 3 and 4 . Aim the protective gas nozzle at the welding ...
Embodiment approach 2
[0030] Embodiment 2: The clamping of the materials to be welded is as follows figure 1 As shown, it is a single pulse current welding process. Thermal compensation block 2 is No. 45 steel with a thickness of 1mm. AZ31 magnesium alloy workpiece 3 is the overlap of two flat plates with a thickness of 0.4mm. Mix 38 parts of active powder 100 mesh titanium dioxide, 42 parts of 50 mesh silicon dioxide, and the remaining 150 mesh calcium fluoride medium with alcohol, and then evenly spray it on the surface of the magnesium alloy workpiece 3 to be welded by a pressure sprayer to form a powder Dielectric fill layer 4. The main welding parameters are set as follows: welding current I = 5000A, electrode pressure = 1560N, welding current duration t2 = 1.3s. After the acetone in the powder filling layer is volatilized, the flat workpieces to be welded are lapped and clamped between the upper and lower electrodes. Aim the protective gas nozzle at the welding area, turn on the argon gas...
Embodiment approach 3
[0031] Embodiment 3: The clamping of the materials to be welded is as follows figure 1 As shown, it is a single pulse current welding process. The thermal compensation block is 45 steel with a thickness of 1mm. AZ31 magnesium alloy workpiece 3 is the overlap of two flat plates with a thickness of 1mm. Mix 38 parts of active powder 50-mesh titanium dioxide, 42 parts of 100-mesh silicon dioxide, and the rest 50-mesh calcium fluoride medium with alcohol, and then evenly spray it on the surface of the magnesium alloy workpiece 3 to be welded by a pressure sprayer to form a powder Dielectric fill layer 4. The main welding parameters are set as follows: welding current I = 5500A, electrode pressure = 1960N, welding current duration t2 = 2s. After the acetone in the powder filling layer is volatilized, the flat workpieces to be welded are lapped and clamped between the upper and lower electrodes. Aim the protective gas nozzle at the welding area, turn on the argon gas protection...
PUM
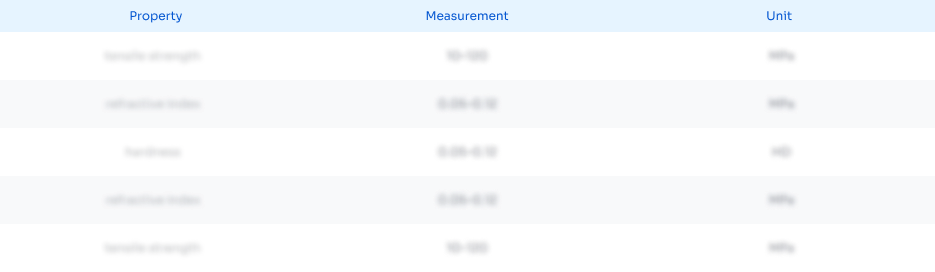
Abstract
Description
Claims
Application Information

- R&D
- Intellectual Property
- Life Sciences
- Materials
- Tech Scout
- Unparalleled Data Quality
- Higher Quality Content
- 60% Fewer Hallucinations
Browse by: Latest US Patents, China's latest patents, Technical Efficacy Thesaurus, Application Domain, Technology Topic, Popular Technical Reports.
© 2025 PatSnap. All rights reserved.Legal|Privacy policy|Modern Slavery Act Transparency Statement|Sitemap|About US| Contact US: help@patsnap.com