Steel 18MnMoNbR for pressure vessel and process for producing 18MnMoNbR steel plate with thickness of 100mm
A pressure vessel and production process technology, applied in the field of pressure vessel steel 18MnMoNbR and its 100mm thick plate production process, can solve the problems of difficult production and high production cost
- Summary
- Abstract
- Description
- Claims
- Application Information
AI Technical Summary
Problems solved by technology
Method used
Image
Examples
Embodiment 1
[0020] A pressure vessel steel 18MnMoNbR, containing the following chemical composition in mass percent (unit, wt%): C: 0.16, Si: 0.25, Mn: 1.35, Mo: 0.5, P≤0.015, S≤0.005, Als: 0.015, Nb : 0.030, Ti: 0.010, others are Fe and residual elements.
[0021] The carbon equivalent of the chemical composition is ≤0.40.
[0022] The pressure vessel steel 18MnMoNbR has 90% tempered bainite and 10% ferrite.
[0023] Further, a production process for producing 100mm pressure vessel steel 18MnMoNbR thick plate is provided, which includes the following steps:
[0024] a. KR molten iron pretreatment: The molten iron at the station must remove the front slag and the rear slag to ensure that the thickness of the slag layer on the liquid surface is ≤20mm. ℃;
[0025] b. Converter smelting: S ≤ 0.003% and P ≤ 0.080% of the molten iron into the furnace, the temperature of the molten iron is 1270°C, the error of the amount of molten iron is controlled by ± 1t, the scrap steel is strictly...
Embodiment 2
[0044] A pressure vessel steel 18MnMoNbR, containing the following chemical composition in mass percent (unit, wt%): C: 0.18, Si: 0.35, Mn: 1.40, Mo: 0.55, P≤0.015, S≤0.005, Als: 0.025, Nb : 0.035, Ti: 0.015, others are Fe and residual elements.
[0045] The carbon equivalent of the chemical composition is ≤0.40.
[0046] The pressure vessel steel 18MnMoNbR has 90% tempered bainite and 10% ferrite.
[0047] Further, a production process for producing 100mm pressure vessel steel 18MnMoNbR thick plate is provided, which includes the following steps:
[0048] a. KR molten iron pretreatment: The molten iron must be removed before and after the slag is removed to ensure that the thickness of the slag layer on the liquid surface is ≤20mm. ℃;
[0049] b. Converter smelting: S ≤ 0.003% and P ≤ 0.080% of the molten iron into the furnace, the temperature of the molten iron is 1290°C, the error of the amount of molten iron is controlled by ±1t, the scrap steel is strictly made o...
Embodiment 3
[0068] A pressure vessel steel 18MnMoNbR, containing the following chemical composition in mass percent (unit, wt%): C: 0.20, Si: 0.45, Mn: 1.45, Mo: 0.6, P≤0.015, S≤0.005, Als: 0.040, Nb : 0.040, Ti: 0.020, others are Fe and residual elements.
[0069] The carbon equivalent of the chemical composition is ≤0.40.
[0070] The pressure vessel steel 18MnMoNbR has 90% tempered bainite and 10% ferrite.
[0071] Further, a production process for producing 100mm pressure vessel steel 18MnMoNbR thick plate is provided, which includes the following steps:
[0072]a. KR molten iron pretreatment: The molten iron at the station must remove the front slag and the rear slag to ensure that the thickness of the slag layer on the liquid surface is ≤20mm. ℃;
[0073] b. Converter smelting: S ≤ 0.003% and P ≤ 0.080% of the molten iron into the furnace, the temperature of the molten iron is 1310°C, the error of the amount of molten iron is controlled by ± 1t, the scrap steel is strictly ma...
PUM
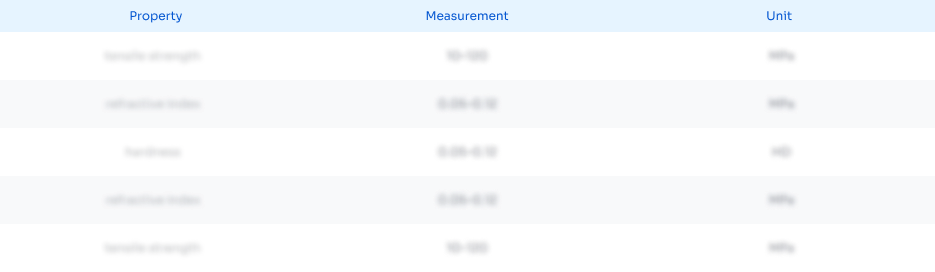
Abstract
Description
Claims
Application Information

- Generate Ideas
- Intellectual Property
- Life Sciences
- Materials
- Tech Scout
- Unparalleled Data Quality
- Higher Quality Content
- 60% Fewer Hallucinations
Browse by: Latest US Patents, China's latest patents, Technical Efficacy Thesaurus, Application Domain, Technology Topic, Popular Technical Reports.
© 2025 PatSnap. All rights reserved.Legal|Privacy policy|Modern Slavery Act Transparency Statement|Sitemap|About US| Contact US: help@patsnap.com