Electrolytic copper-powder-processing technique
A technology of electrolytic copper powder and electrolytic method, which is applied in the production of copper powder and the field of copper powder production by electrolytic method, which can solve the problems of low product yield, high labor intensity, poor effect, etc., and achieve shortened process flow and automation High, remarkable energy-saving effect
- Summary
- Abstract
- Description
- Claims
- Application Information
AI Technical Summary
Problems solved by technology
Method used
Image
Examples
Embodiment 1
[0022] A process for producing copper powder by electrolysis, such as figure 1 shown, proceed as follows:
[0023] (1), first carry out copper powder electrolysis;
[0024] (2) The copper powder is transported to the washing and dehydrating machine by industrial hose pump;
[0025] (3) Powder brushing: automatic powder brushing machine is adopted, the form of powder brushing on the cathode: two ups and two downs, the powder brushing time is 20 seconds, the stepping time of the powder brushing machine is 10 seconds, and the powder brushing cycle is 30 minutes;
[0026] (4) Integrated process of automatic filtration, washing, saponification and dehydration of electrolytic copper powder: after the mixture of electrolytic copper powder and electrolyte enters the washing and dehydrating machine, the electrolyte is filtered out by compressed air, and then passes through 2 to 3 times of dilute solution Washing and filtering, 2 to 3 times of pure water washing and filtering, saponif...
PUM
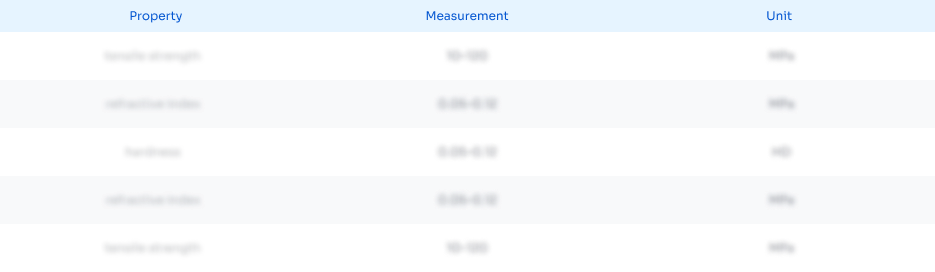
Abstract
Description
Claims
Application Information

- R&D Engineer
- R&D Manager
- IP Professional
- Industry Leading Data Capabilities
- Powerful AI technology
- Patent DNA Extraction
Browse by: Latest US Patents, China's latest patents, Technical Efficacy Thesaurus, Application Domain, Technology Topic, Popular Technical Reports.
© 2024 PatSnap. All rights reserved.Legal|Privacy policy|Modern Slavery Act Transparency Statement|Sitemap|About US| Contact US: help@patsnap.com