Method for obtaining tri-modal microstructure in dual-phase titanium alloy through furnace cooling
A titanium alloy and microstructure technology, applied in the field of titanium alloy thermal processing, can solve the problems of small thickness of secondary sheet α, narrow temperature range, inconvenient forging temperature, etc.
- Summary
- Abstract
- Description
- Claims
- Application Information
AI Technical Summary
Problems solved by technology
Method used
Image
Examples
Embodiment 1
[0015] This embodiment is a method for obtaining a titanium alloy with a three-state structure through furnace cooling. The sample used is a TA15 titanium alloy, and the shape of the sample is cylindrical. The specification of the sample is Φ10*15mm; the TA15 titanium alloy is Ti-6Al-2Zr-1Mo-1V. The β transformation point of TA15 titanium alloy is 990°C, and the initial structure is equiaxed.
[0016] The specific implementation steps of this embodiment are:
[0017] Step 1, heat preservation and water cooling near the β temperature.
[0018] Heat the resistance furnace to the near β temperature of the TA15 titanium alloy, that is, the temperature range of 10-20°C lower than the β transformation point. In this embodiment, the temperature of the resistance furnace is 975° C., which is 15° C. lower than the beta temperature of the TA15 titanium alloy. When the temperature of the resistance furnace reaches 975°C, put the cylindrical sample into the resistance furnace. Heat th...
Embodiment 2
[0026] This embodiment is a method for obtaining a titanium alloy with a three-state structure through furnace cooling. The sample used is a TA15 titanium alloy. The shape of the sample is cylindrical, and the specification of the sample is Φ55*70mm; the TA15 titanium alloy is Ti-6Al-2Zr-1Mo-1V. The β transformation point of TA15 titanium alloy is 990°C, and the initial structure is a two-state structure.
[0027] The specific implementation steps of this embodiment are:
[0028] Step 1, heat preservation and water cooling near the β temperature. The resistance furnace is heated to the near β temperature of the TA15 titanium alloy, that is, the temperature range is 10-20°C lower than the β transformation point. In this embodiment, the temperature of the resistance furnace is 970°C, which is 20°C lower than the β temperature of the TA15 titanium alloy. When the temperature of the resistance furnace reaches 970°C, put the cylindrical sample into the resistance furnace. Heat t...
Embodiment 3
[0032] This embodiment is a method for obtaining a three-state structure in a titanium alloy. The sample used is a TC4 titanium alloy. The shape of the sample is cylindrical, and the specification of the sample is Φ30*45mm; the TC4 titanium alloy is Ti -6Al-4V. The β transformation point of TC4 titanium alloy is 985°C, and the initial structure is equiaxed.
[0033] The specific implementation steps of this embodiment are:
[0034] Step 1, heat preservation and water cooling near the β temperature. The resistance furnace is heated to the near β temperature of the TC4 titanium alloy, that is, the temperature range is 10-20°C lower than the β transformation point. In this embodiment, the temperature of the resistance furnace is 975°C, which is 10°C lower than the β temperature of the TC4 titanium alloy. When the temperature of the resistance furnace reaches 975°C, put the cylindrical sample into the resistance furnace. Heat the resistance furnace to 975°C and start heat prese...
PUM
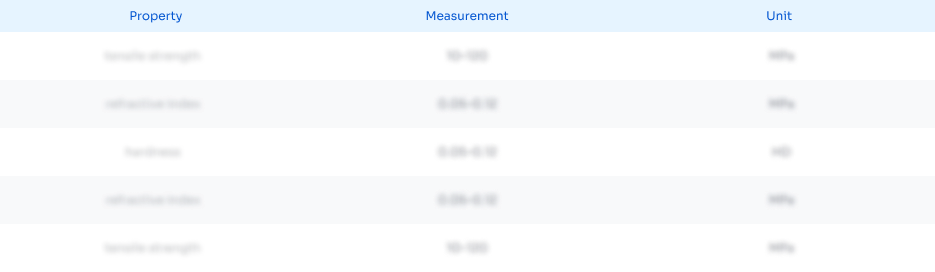
Abstract
Description
Claims
Application Information

- R&D
- Intellectual Property
- Life Sciences
- Materials
- Tech Scout
- Unparalleled Data Quality
- Higher Quality Content
- 60% Fewer Hallucinations
Browse by: Latest US Patents, China's latest patents, Technical Efficacy Thesaurus, Application Domain, Technology Topic, Popular Technical Reports.
© 2025 PatSnap. All rights reserved.Legal|Privacy policy|Modern Slavery Act Transparency Statement|Sitemap|About US| Contact US: help@patsnap.com