Fan-shaped spray head structure for vapor phase epitaxy of material
A vapor phase epitaxy, fan-shaped nozzle technology, applied in metal material coating process, gaseous chemical plating, chemical reactive gas and other directions, to achieve the effect of good use and improve production efficiency
- Summary
- Abstract
- Description
- Claims
- Application Information
AI Technical Summary
Problems solved by technology
Method used
Image
Examples
Embodiment 1
[0033] Reactions involving chemical vapor deposition (CVD) or hydride vapor phase epitaxy (HVPE) require high temperature conditions. Therefore, the material of the nozzle needs to be selected with high strength, no chemical reaction with the reaction gas, and a material with a low thermal expansion coefficient, such as the nozzle made of quartz, see the attached image 3 .
[0034] The intake pipe of the quartz nozzle is determined by the number of isolation areas below, and the isolation area requires at least three, that is, in NH 3 Add N between GaCl and 2 as an insulating gas. Therefore, the number of intake pipes is at least three, and the three intake pipes are independent of each other, and the intake flow is controllable.
[0035] When the number of isolated areas is three, the gas enters the isolated areas from the intake pipe and is separated, then split or preheated, and then sprayed out from the nozzle.
[0036] Since the middle area of the nozzle is fed wit...
Embodiment 2
[0039] Reactions involving chemical vapor deposition (CVD) or hydride vapor phase epitaxy (HVPE) require high temperature conditions. Therefore, the nozzle material needs to be high-strength, does not chemically react with the reaction gas, and has a low thermal expansion coefficient, such as the nozzle made of quartz, see the attached Figure 4 .
[0040] The intake pipe of the quartz nozzle is determined by the number of isolation areas below, and the isolation area requires at least three, that is, in the NH 3 Add N between GaCl and 2 as a shielding gas. Therefore, the number of intake pipes is at least three, and the three intake pipes are independent of each other, and the intake flow is controllable.
[0041] If the number of isolation areas is increased to five, that is, in NH 3 Add a N on the outside of GaCl and GaCl 2 isolation area (i.e. each sprinkler has 3 N 2 isolation zone), the shunted and preheated NH 3 Within a short distance after the GaCl gas is eject...
Embodiment 3
[0044] Reactions involving chemical vapor deposition (CVD) or hydride vapor phase epitaxy (HVPE) require high temperature conditions. Therefore, the nozzle material needs to be high-strength, does not chemically react with the reaction gas, and has a low thermal expansion coefficient, such as the nozzle made of quartz, see the attached Figure 5 .
[0045] The intake pipe of the quartz nozzle is determined by the number of isolation areas below, and the isolation area requires at least three, that is, in the NH 3 Add N between GaCl and 2 as a shielding gas. Therefore, the number of intake pipes is at least three, and the three intake pipes are independent of each other, and the intake flow is controllable.
[0046] When the number of isolated areas is three, the gas enters the isolated area from the intake pipe and is separated, then split or preheated, and then sprayed out from the nozzle.
[0047] Since the middle area of the nozzle is fed with N 2 , so NH3 and GaCl d...
PUM
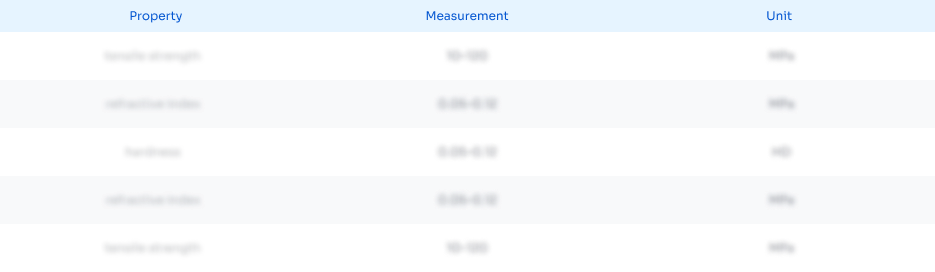
Abstract
Description
Claims
Application Information

- R&D
- Intellectual Property
- Life Sciences
- Materials
- Tech Scout
- Unparalleled Data Quality
- Higher Quality Content
- 60% Fewer Hallucinations
Browse by: Latest US Patents, China's latest patents, Technical Efficacy Thesaurus, Application Domain, Technology Topic, Popular Technical Reports.
© 2025 PatSnap. All rights reserved.Legal|Privacy policy|Modern Slavery Act Transparency Statement|Sitemap|About US| Contact US: help@patsnap.com