Thermal field structure for casting polycrystalline silicon ingot
A polycrystalline silicon ingot and thermal field technology, which is applied in the directions of polycrystalline material growth, crystal growth, single crystal growth, etc., can solve the problems of low conversion efficiency and battery conversion efficiency, so as to improve conversion efficiency, reduce crystal defects, and suppress crystal The effect of defect generation
- Summary
- Abstract
- Description
- Claims
- Application Information
AI Technical Summary
Problems solved by technology
Method used
Image
Examples
Embodiment
[0019] Such as Figure 2-3 As shown, a thermal field structure for casting polycrystalline silicon ingots includes a quartz crucible 1, a heat insulation plate 2, a side heater 9, a heat insulation layer 6, and a heat exchange platform 5, and the quartz crucible 1 is arranged on the heat exchange platform 5 Above, the outer wall of the crucible is provided with a crucible guard plate 12, the quartz crucible 1 is surrounded by a heat shield 2, the heat shield 1 is provided with a side heat insulation layer 6, and a side heater is provided between the two. 9. The distance between the outer wall of the heat shield 2 and the side heater 9 is greater than 1 cm, and the distance between the inner wall and the outer wall of the quartz crucible 1 is less than 5 cm, and the heat shield 2 is fixed on the side heat insulation layer 6 bottom, the upper part of the quartz crucible 1 is provided with an upper heat insulating layer 7, the lower part is provided with a lower heat insulating l...
PUM
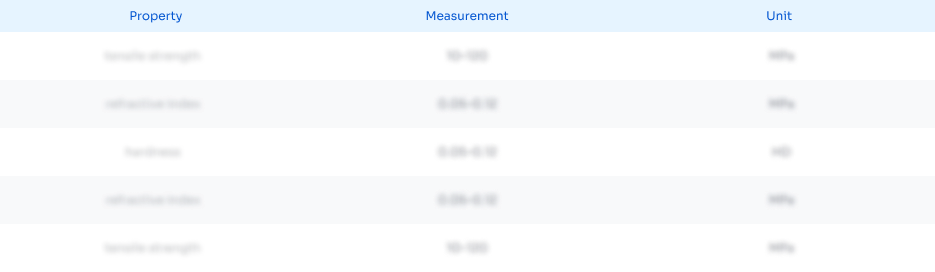
Abstract
Description
Claims
Application Information

- Generate Ideas
- Intellectual Property
- Life Sciences
- Materials
- Tech Scout
- Unparalleled Data Quality
- Higher Quality Content
- 60% Fewer Hallucinations
Browse by: Latest US Patents, China's latest patents, Technical Efficacy Thesaurus, Application Domain, Technology Topic, Popular Technical Reports.
© 2025 PatSnap. All rights reserved.Legal|Privacy policy|Modern Slavery Act Transparency Statement|Sitemap|About US| Contact US: help@patsnap.com