Preparation method and application of Fe and Cu composite molecular sieve catalyst
A composite molecular sieve and catalyst technology, which is applied in the direction of molecular sieve catalysts, separation methods, chemical instruments and methods, etc., can solve the problems of not having a reaction temperature window and being unable to meet the complex and changeable reaction conditions in the field of environmental catalysis, so as to reduce pollution and expand Operating temperature window, effect of improving performance
- Summary
- Abstract
- Description
- Claims
- Application Information
AI Technical Summary
Problems solved by technology
Method used
Image
Examples
Embodiment 1
[0019] The preparation method of the catalyst of the present embodiment comprises the following steps:
[0020] Step 1. Preparation of Fe molecular sieve catalyst
[0021] Measure 250mL of deionized water, add 8g of ZSM-5 molecular sieve, the SiO 2 / Al 2 O 3 is 23, stir at room temperature; then add 3 g of FeCl according to the stoichiometric ratio 2 , and stirred at room temperature for 24 hours to carry out ion exchange; then washed with deionized water and suction filtered, and the obtained filter cake was first dried in an oven for 12 hours; finally, it was calcined in a muffle furnace at 550 °C for 4 hours to obtain Fe-ZSM-5 molecular sieve catalyst.
[0022] Step 2. Preparation of Cu molecular sieve catalyst
[0023] Measure 250mL of deionized water, add 8g of ZSM-5 molecular sieve, the SiO 2 / Al 2 O 3 is 23, stir at room temperature; then add 3 g of Cu(NO) according to the stoichiometric ratio 3 ) 2 , stirred at room temperature for 24 hours, and carried out io...
Embodiment 2
[0030] The preparation method of the catalyst of the present embodiment comprises the following steps:
[0031] Step 1. Preparation of Fe molecular sieve catalyst
[0032] Measure 250mL of deionized water, add 8g of ZSM-5 molecular sieve, the SiO 2 / Al 2 O 3 is 23, stir at room temperature; then add 3 g of FeCl according to the stoichiometric ratio 2 , and stirred at room temperature for 24 hours to carry out ion exchange; then washed with deionized water and suction filtered, and the obtained filter cake was first dried in an oven for 12 hours; finally, it was calcined in a muffle furnace at 550 °C for 4 hours to obtain Fe-ZSM-5 molecular sieve catalyst.
[0033] Step 2. Preparation of Cu molecular sieve catalyst
[0034]Measure 250mL of deionized water, add 8g of ZSM-5 molecular sieve, the SiO 2 / Al 2 O 3 is 23, stir at room temperature; then add 3 g of Cu(NO) according to the stoichiometric ratio 3 ) 2 , stirred at room temperature for 24 hours, and carried out ion...
Embodiment 3
[0041] The preparation method of the catalyst of the present embodiment comprises the following steps:
[0042] Step 1. Preparation of Fe molecular sieve catalyst
[0043] Measure 250mL of deionized water, add 8g of ZSM-5 molecular sieve, the SiO 2 / Al 2 O 3 is 23, stir at room temperature; then add 3 g of FeCl according to the stoichiometric ratio 2 , and stirred at room temperature for 24 hours to carry out ion exchange; then washed with deionized water and suction filtered, and the obtained filter cake was first dried in an oven for 12 hours; finally, it was calcined in a muffle furnace at 550 °C for 4 hours to obtain Fe-ZSM-5 molecular sieve catalyst.
[0044] Step 2. Preparation of Cu molecular sieve catalyst
[0045] Measure 250 mL of deionized water, add 8 g of SSZ-13 molecular sieve, and stir at room temperature; then add 3 g of Cu(NO) according to the stoichiometric ratio 3 ) 2 , and stirred at room temperature for 24 hours to perform ion exchange; then washed w...
PUM
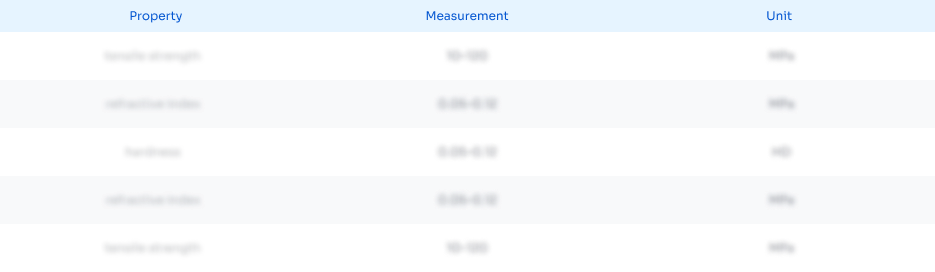
Abstract
Description
Claims
Application Information

- R&D
- Intellectual Property
- Life Sciences
- Materials
- Tech Scout
- Unparalleled Data Quality
- Higher Quality Content
- 60% Fewer Hallucinations
Browse by: Latest US Patents, China's latest patents, Technical Efficacy Thesaurus, Application Domain, Technology Topic, Popular Technical Reports.
© 2025 PatSnap. All rights reserved.Legal|Privacy policy|Modern Slavery Act Transparency Statement|Sitemap|About US| Contact US: help@patsnap.com