Body contact forming method by utilizing SOI (silicon on insulator) MOSFET (metal oxide semiconductor field effect transistor) of sacrificial layer
A body contact and sacrificial layer technology, applied in semiconductor/solid-state device manufacturing, electrical components, circuits, etc., can solve problems such as cumbersome manufacturing steps, complicated device manufacturing processes, and damage to the isolation effect of SOIMOSFET devices.
- Summary
- Abstract
- Description
- Claims
- Application Information
AI Technical Summary
Problems solved by technology
Method used
Image
Examples
Embodiment Construction
[0027] Hereinafter, the present invention will be described in detail with examples in conjunction with the drawings:
[0028] Combine figure 1 . The buried SiO is deposited on the underlying semiconductor substrate 1 as shown 2 Layer 2, buried in SiO 2 A SiGe masking film 3 is deposited on the layer 2. The material of the underlying semiconductor substrate 1 can be freely selected, for example: silicon, germanium, group III~V compound semiconductor materials, group II~VI compound semiconductor materials or other compound semiconductor materials, etc., and single crystal materials can also be used. It can be made into an n-type substrate or a p-type substrate by doping.
[0029] Combine figure 2 . Coat the photoresist 4 on the SiGe masking film 3 so that the photoresist 4 covers a small part of the SiGe masking film 3, and remove the uncoated SiGe masking film 3 by etching until the buried SiO is exposed 2 Layer 2, and the remaining SiGe masking film 3a on both sides of the buri...
PUM
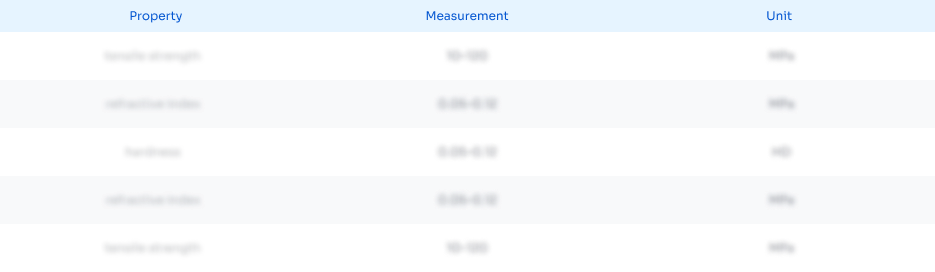
Abstract
Description
Claims
Application Information

- R&D
- Intellectual Property
- Life Sciences
- Materials
- Tech Scout
- Unparalleled Data Quality
- Higher Quality Content
- 60% Fewer Hallucinations
Browse by: Latest US Patents, China's latest patents, Technical Efficacy Thesaurus, Application Domain, Technology Topic, Popular Technical Reports.
© 2025 PatSnap. All rights reserved.Legal|Privacy policy|Modern Slavery Act Transparency Statement|Sitemap|About US| Contact US: help@patsnap.com