Method for separating and recycling casting residues
A technology for separation and recovery of casting slag, applied in the direction of recycling technology, casting equipment, process efficiency improvement, etc., can solve the problem of high separation cost, achieve the effect of simple process, improved separation efficiency of slag and iron, and increased fluidity
- Summary
- Abstract
- Description
- Claims
- Application Information
AI Technical Summary
Problems solved by technology
Method used
Image
Examples
Embodiment 1
[0041] The method for separating and reclaiming casting residue and molten steel in common slag pots comprises the following steps:
[0042] 1) Spread 50kg of waste sand from the heating furnace with a particle size of <3mm evenly into the 80t empty slag tank first to prevent the phenomenon of welding with the bottom of the slag tank after the layered sinking of residual steel.
[0043] 2) After the continuous casting of a tank of molten steel is completed, use a crane to lift the cast ladle away from the ladle turret, and then pour the high-temperature casting slag and residual molten steel in the ladle into the empty slag that has been added to the waste sand of the heating furnace Can.
[0044] 3) Add 560kg of waste sand from the heating furnace with a particle size of <3mm to the surface of the casting residue in the slag tank to cover. The waste sand of the heating furnace reacts with the high-temperature casting slag to form a low-alkalinity slag with a reduced melting ...
Embodiment 2
[0053] The method for separating and reclaiming casting residue and molten steel in common slag pots comprises the following steps:
[0054] 1) Spread 50kg of fly ash with a particle size of <1mm evenly into the 80t empty slag tank first to prevent the phenomenon of welding with the bottom of the slag tank after the layered sinking of residual steel.
[0055] 2) After the continuous casting of a tank of molten steel is completed, use a crane to lift the cast ladle away from the ladle turret, and then pour the high-temperature casting slag and residual molten steel in the ladle into the empty slag that has been added with fly ash Can.
[0056] 3) Then add 810kg of fly ash with a particle size of <1mm to the surface of the casting slag in the slag tank to cover. Fly ash reacts with high-temperature casting slag to form low-alkalinity slag with lower melting point and enhanced fluidity.
[0057] 4) Under the action of gravity and surface tension, let it stand for 40 minutes to ma...
PUM
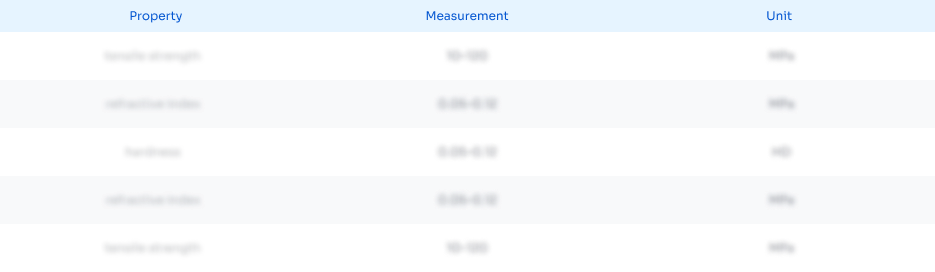
Abstract
Description
Claims
Application Information

- Generate Ideas
- Intellectual Property
- Life Sciences
- Materials
- Tech Scout
- Unparalleled Data Quality
- Higher Quality Content
- 60% Fewer Hallucinations
Browse by: Latest US Patents, China's latest patents, Technical Efficacy Thesaurus, Application Domain, Technology Topic, Popular Technical Reports.
© 2025 PatSnap. All rights reserved.Legal|Privacy policy|Modern Slavery Act Transparency Statement|Sitemap|About US| Contact US: help@patsnap.com