Technique for producing high-purity PET (polyethylene terephthalate) granules from waste reflecting films
A process method and technology of reflective film, applied in the field of waste material utilization, can solve the problems of personal electrocution, affecting the safe operation of the power grid, etc., and achieve the effect of eliminating hidden safety hazards, improving industrial value, and huge social and economic benefits.
- Summary
- Abstract
- Description
- Claims
- Application Information
AI Technical Summary
Problems solved by technology
Method used
Examples
Embodiment 1
[0022] Embodiment 1: a kind of processing method utilizing waste and old reflective film to produce high-purity PET pellet, it comprises the steps:
[0023] a. First, clean the waste reflective film and crush it until the length of the reflective film is less than 1cm;
[0024] B. adopt the sodium stearate emulsion that weight concentration is 2% to go out the reflective layer of reflective film, the weight ratio of sodium stearate emulsion and reflective film is 8:1;
[0025] c. Separate and recycle the removed reflective film waste by filtering, and dry at 60°C for 6 hours;
[0026] d. Add 2 parts of plasticizer octyl phthalate and 4 parts of petrolatum in 100 parts of reflective film material after separation and recovery by weight and stir evenly;
[0027] e. Add 0.18 parts of sucrose, 0.22 parts of glycerin and 2.6 parts of linear low density polyethylene in parts by weight to 100 parts of reflective film that has been stirred evenly;
[0028] f. Add 0.1 part of tribasi...
Embodiment 2
[0030] Embodiment 2: a kind of processing method utilizing waste and old reflective film to produce high-purity PET grain, it comprises the steps:
[0031] a. First, clean the waste reflective film and crush it until the length of the reflective film is less than 1cm;
[0032] B. Adopt the fatty acid surfactant emulsion that weight concentration is 8% to go out the reflective layer of reflective film, the weight ratio of fatty acid surfactant emulsion and reflective film is 12:1; Fatty acid surfactant emulsion is magnesium stearate, polyethylene Mixed water emulsion of glycol 2000 and polyethylene glycol 4000;
[0033] c. Separate and recover the removed reflective film waste by filtering, and dry at 80°C for 4 hours;
[0034] d. Add 2 parts of dimethyl phthalate, 2 parts of diethyl phthalate, 8 parts of petrolatum, 1 part of lead stearate, 1 part of reflective film material by weight in 100 parts of reflective film materials after separation and recovery. Parts of calcium s...
Embodiment 3
[0038] Embodiment 3: a kind of processing method utilizing waste and old reflective film to produce high-purity PET grain, it comprises the steps:
[0039] a. First, clean the waste reflective film and crush it until the length of the reflective film is less than 1cm;
[0040] B. Adopt the polyethylene glycol 6000 emulsion that weight concentration is 5% to come out of the reflective layer of reflective film, the weight ratio of polyethylene glycol 6000 emulsion and reflective film is 10:1;
[0041] c. Separate and recover the removed reflective film waste by filtering, and dry at 70°C for 5 hours;
[0042] d. Add 3 parts of octyl phthalate and 6 parts of glyceride, 0.6 part of lead stearate, 0.4 part of calcium stearate in parts by weight in 100 parts of reflective film materials after separation and recovery and stir evenly;
[0043] e. Add 0.5 part of sucrose, 0.6 part of glycerin, and 5 parts of linear low-density polyethylene to the mixture of 100 parts of reflective fil...
PUM
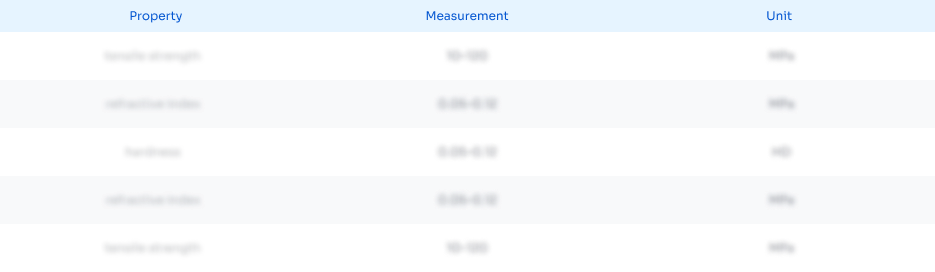
Abstract
Description
Claims
Application Information

- R&D
- Intellectual Property
- Life Sciences
- Materials
- Tech Scout
- Unparalleled Data Quality
- Higher Quality Content
- 60% Fewer Hallucinations
Browse by: Latest US Patents, China's latest patents, Technical Efficacy Thesaurus, Application Domain, Technology Topic, Popular Technical Reports.
© 2025 PatSnap. All rights reserved.Legal|Privacy policy|Modern Slavery Act Transparency Statement|Sitemap|About US| Contact US: help@patsnap.com