Foamed aluminum sandwich board bend forming method
A bending forming and sandwich panel technology, which is applied in laser welding equipment, manufacturing tools, welding equipment, etc., can solve the problems of complex processing devices, inability to use foamed aluminum sandwich panels for bending forming, unfavorable laser bending forming, etc., and achieve high Produce flexibility, avoid oxidation effect
- Summary
- Abstract
- Description
- Claims
- Application Information
AI Technical Summary
Problems solved by technology
Method used
Image
Examples
Embodiment 1
[0026] Embodiment one: see figure 1 As shown, the schematic diagram of the device used in this embodiment is shown in the figure. The processing device includes a workbench 4 and a chuck 3 located on the workbench. The aluminum foam sandwich panel is clamped by the chuck, and the upper surface is drawn with processing In a straight line, the laser beam 1 and the shielding gas conduit 6 move synchronously along the scanning direction 5, or the chuck drives the aluminum foam sandwich panel to move. Nitrogen gas is injected into the shielding gas conduit 6 .
[0027] CO was carried out on the 80×20×10mm aluminum foam sandwich panel with a porosity of 80%. 2 Laser scanning, the scanning line position is at the center of the plate, the length is 20mm, the laser power is 150W, scanning is performed 10 times, and the scanning rate is 8mm / s. The operation steps are as follows: (1) Use black hand spray paint to spray on the scanning area, and use the clamp to clamp on one side. (2) ...
Embodiment 2
[0029] Embodiment 2: Using the same device as in Embodiment 1, CO 2 Laser scanning, the scanning line position is in the center of the plate, the length is 20mm, the laser power is 150W and the scanning rate is 8mm / s for 15 times. The operation steps are as follows: (1) Use black hand spray paint to spray on the scanning area, and use the clamp to clamp on one side. (2) The scanning speed is 8mm / S scanning at a constant speed, and the laser bending is realized through the laser numerical control processing system. (3) After completely cooling naturally, use a laser displacement sensor to measure the deformation angle.
[0030] After processing in this embodiment, the bending angle of the plate is 6 degrees.
[0031] By increasing the number of scans, the bending angle of the sheet can be increased.
PUM
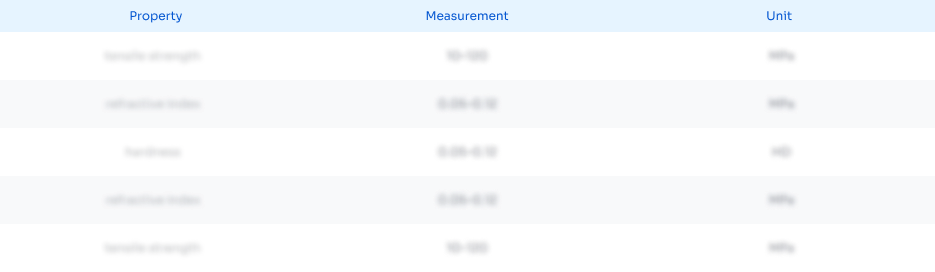
Abstract
Description
Claims
Application Information

- R&D Engineer
- R&D Manager
- IP Professional
- Industry Leading Data Capabilities
- Powerful AI technology
- Patent DNA Extraction
Browse by: Latest US Patents, China's latest patents, Technical Efficacy Thesaurus, Application Domain, Technology Topic, Popular Technical Reports.
© 2024 PatSnap. All rights reserved.Legal|Privacy policy|Modern Slavery Act Transparency Statement|Sitemap|About US| Contact US: help@patsnap.com