Camera-based real-time shooting 3D printing process monitoring method and device
A technology of real-time shooting and 3D printing, which is applied in the direction of improving process efficiency, improving energy efficiency, and additive manufacturing. It can solve problems such as high technical threshold, increase the difficulty of real-time monitoring of molten pool, and put forward high requirements, so as to achieve optimized process. Parameters, simple structure, and the effect of improving accuracy
- Summary
- Abstract
- Description
- Claims
- Application Information
AI Technical Summary
Problems solved by technology
Method used
Image
Examples
Embodiment
[0032] Such as figure 1 , figure 2 shown. The invention discloses a 3D printing process monitoring device based on camera real-time shooting, which includes a sealed molding room, a camera 1 is installed on the upper part of the sealed molding room, and the camera 1 monitors the shape of the 3D printing melting layer process through an opening in the upper part of the sealed molding room. A light source 7 is installed on the inner side of the top of the sealed molding chamber; the light source 7 is pulsed on when the camera 1 is exposed, and the light source 7 is turned off after the camera 1 is exposed, and the camera 1 transmits the layer shape data to the computer 6 in real time and store.
[0033] The pixel resolution of the camera is 1024×1024, 300 frames per second; the shortest exposure time of the overall shutter is 1us; the dynamic range is 120dB; the spectral range is 400-950nm, and the sampling resolution is 8 bits.
[0034] The light source 7 can be an LED ligh...
PUM
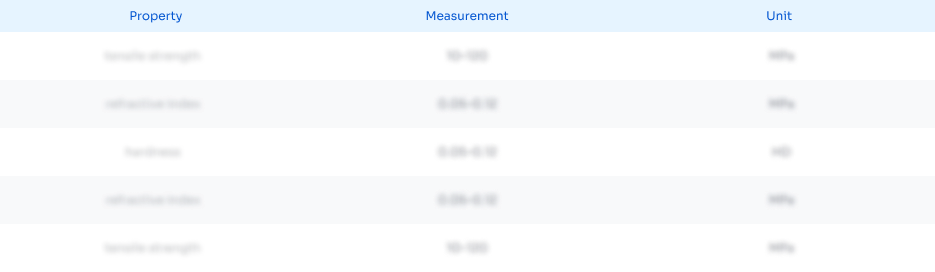
Abstract
Description
Claims
Application Information

- R&D
- Intellectual Property
- Life Sciences
- Materials
- Tech Scout
- Unparalleled Data Quality
- Higher Quality Content
- 60% Fewer Hallucinations
Browse by: Latest US Patents, China's latest patents, Technical Efficacy Thesaurus, Application Domain, Technology Topic, Popular Technical Reports.
© 2025 PatSnap. All rights reserved.Legal|Privacy policy|Modern Slavery Act Transparency Statement|Sitemap|About US| Contact US: help@patsnap.com