Method and device of local heat treatment for thin-walled tubular parts
A local heat treatment and parts technology, applied in heat treatment furnaces, heat treatment equipment, quenching devices, etc., can solve the problems of insufficient local heat treatment, uneven heating, cracking of parts, etc., to overcome uneven heating, save production costs, improve The effect of production efficiency
- Summary
- Abstract
- Description
- Claims
- Application Information
AI Technical Summary
Problems solved by technology
Method used
Image
Examples
Embodiment Construction
[0027] The present invention will be further described in detail below in conjunction with the accompanying drawings and embodiments.
[0028] Embodiments of the present invention: when implementing the method for local heat treatment of a thin-walled tubular part of the present invention, the high-frequency induction heating device in the prior art can be directly used to heat the thin-walled tubular part as the processed part. When performing heat treatment on parts of thin-walled tubular parts, heat treatment shall be carried out according to the following process:
[0029] a. Use a high-frequency induction heating device as the heating source, and determine the inner diameter and heating power of the high-frequency induction coil of the high-frequency induction heating device according to the outer diameter of the heating zone of the thin-walled tubular parts that requires local heat treatment, that is, the high-frequency induction coil. The inner diameter should be 5-30mm...
PUM
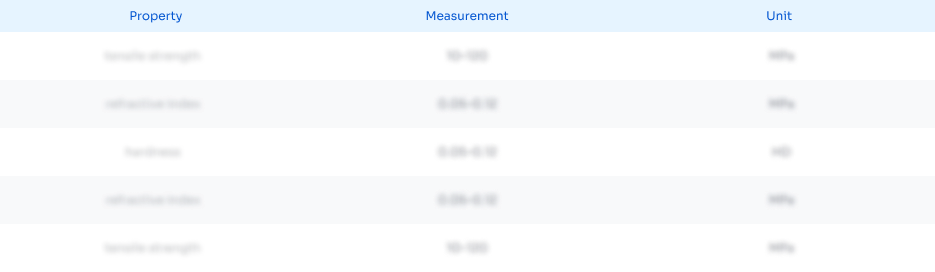
Abstract
Description
Claims
Application Information

- R&D
- Intellectual Property
- Life Sciences
- Materials
- Tech Scout
- Unparalleled Data Quality
- Higher Quality Content
- 60% Fewer Hallucinations
Browse by: Latest US Patents, China's latest patents, Technical Efficacy Thesaurus, Application Domain, Technology Topic, Popular Technical Reports.
© 2025 PatSnap. All rights reserved.Legal|Privacy policy|Modern Slavery Act Transparency Statement|Sitemap|About US| Contact US: help@patsnap.com