Method for producing bimetal composite material by adopting cold core continuous casting and rolling process
A composite material and bimetal technology, applied in metal rolling and other directions, can solve the problems of small selection of materials, large one-time investment, etc., and achieve high-efficiency production process methods, high yield and metal utilization rate, and blank size and shape. Effects with low precision requirements
- Summary
- Abstract
- Description
- Claims
- Application Information
AI Technical Summary
Problems solved by technology
Method used
Image
Examples
Embodiment 1
[0029] as attached figure 1 As shown, the cold core base material 1 and the metal cladding material 3 with different physical, chemical and mechanical properties can be selected according to the specific use requirements of the composite pipe or rod such as acid resistance or alkali resistance, corrosion resistance and oxidation resistance. The base material 1 is a finished metal pipe or bar at normal temperature, and the molten cladding material 3 is evenly and continuously coated on the surface of the cold core base material 1 by using the chilled core roll continuous casting and rolling process, and then compounded by high temperature continuous casting and rolling take shape.
[0030] In the first embodiment of the present invention, the steel-aluminum composite round pipe is produced by cold core continuous casting and rolling technology on a vertical casting and rolling machine. Such as figure 1 As shown, the specific steps are as follows:
[0031] Step 1, cold core...
Embodiment 2
[0039] The second embodiment of the present invention is to produce steel-aluminum composite rods on a vertical casting and rolling machine by adopting cold core continuous casting and rolling technology. Such as figure 2 As shown, the specific steps are as follows:
[0040] Step 1, the cold core base material 1 is made of ordinary carbon steel Q235 finished bar, and its surface is treated by removing scale and degreasing to make its surface clean.
[0041] In step 2, aluminum alloy 3A21 is selected as the metal cladding material 3, and the molten aluminum alloy cladding material is placed in the ladle 4.
[0042] Step 3, use the inlet pinch guide device 2 to send the processed substrate 1 into the round hole of the casting roll 5 along the vertical casting rolling direction. The inside of the casting roll is cooled by circulating water, and the surface of the cold substrate 1 It forms an annular crystallizer with the casting roll pass.
[0043] Step 4, use the ladle 4 to ...
Embodiment 3
[0048] In the third embodiment of the present invention, the steel-aluminum composite pipe is produced by a cold core continuous casting and rolling process on a horizontal casting and rolling machine. Such as image 3 As shown, the specific steps are as follows:
[0049] Step 1, cold core base material 1 is made of ordinary carbon steel Q235 finished steel pipe, and its surface is treated with iron scale removal and degreasing to make its surface clean.
[0050] In step 2, the metal cladding material 3 is made of aluminum alloy 3A21, and the molten aluminum alloy is placed in the ladle 4 .
[0051] Step 3, use the inlet pinch guide device 2 to send the treated base material 1 into the round hole of the casting roll 5 along the horizontal casting direction, and the inside of the casting roll is cooled by circulating water, and the surface of the cold base material 1 and the The casting roll pass forms an annular crystallizer.
[0052] Step 4: Continuously inject the claddin...
PUM
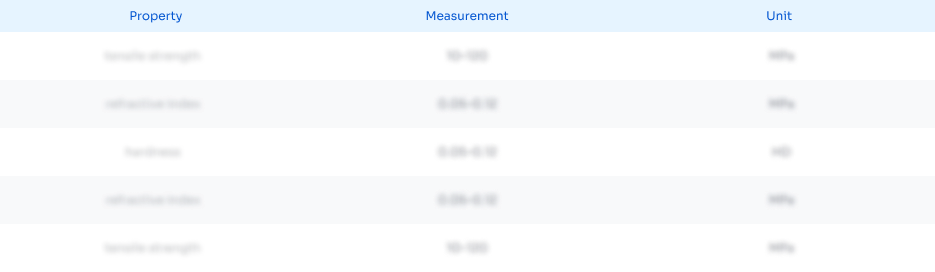
Abstract
Description
Claims
Application Information

- Generate Ideas
- Intellectual Property
- Life Sciences
- Materials
- Tech Scout
- Unparalleled Data Quality
- Higher Quality Content
- 60% Fewer Hallucinations
Browse by: Latest US Patents, China's latest patents, Technical Efficacy Thesaurus, Application Domain, Technology Topic, Popular Technical Reports.
© 2025 PatSnap. All rights reserved.Legal|Privacy policy|Modern Slavery Act Transparency Statement|Sitemap|About US| Contact US: help@patsnap.com