Method for producing rear passivation double-sided solar cell
A double-sided solar cell, backside passivation technology, applied in the direction of circuits, electrical components, final product manufacturing, etc., can solve the problems of limiting the improvement of solar cell efficiency, low cell efficiency, low reflection, etc., to reduce the recombination rate, The effect of good industrial prospects and large production capacity
- Summary
- Abstract
- Description
- Claims
- Application Information
AI Technical Summary
Problems solved by technology
Method used
Image
Examples
Embodiment 1
[0051] Such as figure 1 shown. The steps to realize the present invention can be sequentially as follows: pre-cleaning, texturing→diffusion PN junction→peripheral and backside etching→evaporating SiNx anti-reflection film on the front→evaporating Al on the backside 2 o 3 Passivation film or / and SiNx passivation film or other passivation film → screen printing back electrode → screen printing positive electrode → sintering.
[0052] That is, a method for producing a back passivated double-sided solar cell,
[0053] Generally, it includes the following steps;
[0054] Step 1: Perform pre-cleaning and texturing on the silicon wafer; pre-cleaning is based on removing the damaged layer on the surface of the silicon wafer, and at the same time make a textured surface on the front surface of the battery;
[0055] Step 2: using the above-mentioned silicon wafer as the silicon substrate to deposit a dopant source and perform diffusion to prepare a p-n junction;
[0056] Step 3: Po...
Embodiment 2
[0094] The difference between this example and Example 1 is: firstly, the P silicon wafer is cleaned and textured with a chemical solution, and the damaged layer is removed to form a textured anti-reflection structure; in the diffusion furnace tube, a liquid source of phosphorus oxychloride is used Diffusion to form a P-N junction; use an acid or alkali chemical solution to clean the back junction and surrounding areas, and use a mixed solution of hydrochloric acid, hydrofluoric acid and water to clean the phosphosilicate glass; on the front of the battery, PECVD prepares a silicon nitride film anti-reflection film; On the back of the battery, PECVD prepares aluminum oxide / silicon nitride laminated passivation film;
[0095] Then screen-print grid lines, including back busbars and fine grid lines, and print back bus grids and print fine grid lines at the same time. Both the back bus grid and printed fine grid lines are printed with penetrating silver-aluminum paste to form a pe...
PUM
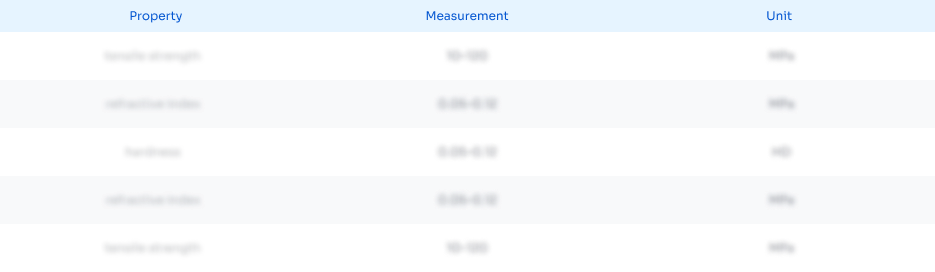
Abstract
Description
Claims
Application Information

- Generate Ideas
- Intellectual Property
- Life Sciences
- Materials
- Tech Scout
- Unparalleled Data Quality
- Higher Quality Content
- 60% Fewer Hallucinations
Browse by: Latest US Patents, China's latest patents, Technical Efficacy Thesaurus, Application Domain, Technology Topic, Popular Technical Reports.
© 2025 PatSnap. All rights reserved.Legal|Privacy policy|Modern Slavery Act Transparency Statement|Sitemap|About US| Contact US: help@patsnap.com