Additive for texturing solution of monocrystalline silicon
A technology of additives and texturing fluid, which is applied in the field of solar cells, can solve the problems of shortening time, pollution, and large amount of isopropanol, and achieve the effects of cost saving, pollution reduction, and short reaction time
- Summary
- Abstract
- Description
- Claims
- Application Information
AI Technical Summary
Problems solved by technology
Method used
Image
Examples
Embodiment 1
[0028] 1) Preparation of additives: Dissolve 1 g of fructose, 50 g of sodium silicate, 60 g of sodium oxalate, 40 g of sodium lactate, and 20 g of nonylphenol polyoxyethylene ether in 829 g of deionized water at room temperature, and stir until completely dissolved to obtain 1000 g of additives.
[0029] 2) Preparation of alkaline texturing solution: 120 g of sodium hydroxide was dissolved in 9.88 kg of deionized water to obtain 10 kg of alkaline texturing solution.
[0030] 3) Add 150g of additives to 10kg of alkaline texturing liquid and mix well.
[0031] 4) Dip the cleaned silicon wafer into the alkaline texturing solution containing additives, and keep the temperature at 80°C for 12 minutes to complete the texturing. The silicon wafer is taken out from the alkaline texturizing solution, washed with deionized water and dried to obtain a blue-black shiny suede surface. The corroded mass of the silicon wafer after texturing is measured by an analytical balance is 0.3539g, ac...
Embodiment 2
[0033] 1) Prepare additives: at room temperature, mix 50g fructose, 35g sodium silicate, 35g sodium acetate, 5g F-containing nonionic surfactant FSO-100 ( , DuPont USA), 15g NP-10 was dissolved in 860g deionized water, stirred until completely dissolved, and 1000g additive was obtained.
[0034] 2) Dissolve 140g of sodium hydroxide in 9.86kg of deionized water to obtain 10kg of alkaline texturing solution.
[0035] 3) Add 30 grams of additives to 10 kg of alkaline texturing liquid and mix well.
[0036] 4) Dip the cleaned silicon wafer into the alkaline texturing solution containing additives, and keep the temperature at 75°C for 18 minutes to complete the texturing. The silicon wafer is taken out from the alkaline texturizing solution, washed with deionized water and dried to obtain a blue-black shiny suede surface. The corroded mass of the silicon wafer after texturing is measured by an analytical balance is 0.3308g, accounting for 4.9% of the mass of the silicon wafer be...
Embodiment 3
[0038] 1) Preparation of additives: at room temperature, mix 50g fructose, 100g sodium silicate, 1g sodium acetate, 1g F-containing nonionic surfactant FSO-100 ( , DuPont, USA) was dissolved in 848g of deionized water and stirred until completely dissolved to obtain 1000g of the additive.
[0039] 2) Dissolve 140g of sodium hydroxide in 9.86kg of deionized water to obtain 10kg of alkaline texturing solution.
[0040] 3) Add 100 grams of additives to 10 kg of alkaline texturing liquid and mix well.
[0041] 4) Dip the cleaned silicon wafer into the alkaline texturing solution containing additives, and keep the temperature at 85°C for 15 minutes to complete the texturing. The silicon wafer is taken out from the alkaline texturizing solution, washed with deionized water and dried to obtain a blue-black shiny suede surface. The corroded mass of the silicon wafer after the texturing is measured by an analytical balance is 0.3903g, accounting for 5.8% of the mass of the silicon w...
PUM
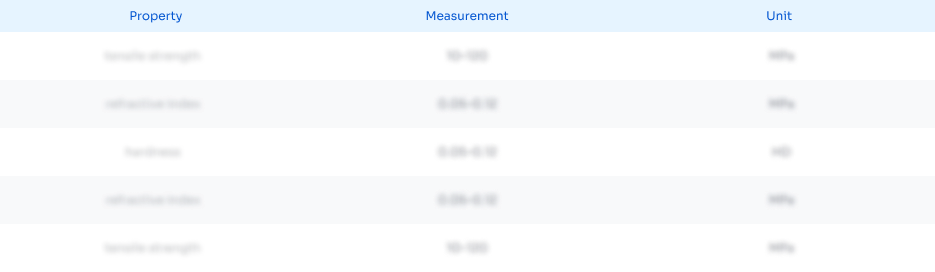
Abstract
Description
Claims
Application Information

- R&D
- Intellectual Property
- Life Sciences
- Materials
- Tech Scout
- Unparalleled Data Quality
- Higher Quality Content
- 60% Fewer Hallucinations
Browse by: Latest US Patents, China's latest patents, Technical Efficacy Thesaurus, Application Domain, Technology Topic, Popular Technical Reports.
© 2025 PatSnap. All rights reserved.Legal|Privacy policy|Modern Slavery Act Transparency Statement|Sitemap|About US| Contact US: help@patsnap.com