Processing modifying agent applied to polyvinyl chloride pipe materials and pipe fittings
A processing modifier and polyvinyl chloride technology, which is used in the field of injection molding processing modifier and extrusion, can solve the problems of poor heat resistance stability and soft pipe fittings, and achieves high stability, narrow particle size distribution and high stability. Effects of uniformity, high hardness and thermal stability
- Summary
- Abstract
- Description
- Claims
- Application Information
AI Technical Summary
Problems solved by technology
Method used
Examples
Embodiment 1
[0021] The air in the reactor equipped with a stirrer and a reflux condenser was replaced with nitrogen. Then, 100 parts by weight of deionized water and 4 parts by weight of sodium dodecyl diphenyl ether disulfonate were added, and stirred evenly. 41 parts by weight of styrene monomer, 7 parts by weight of acrylonitrile monomer, 2 parts by weight The n-butyl methacrylate monomer composition was put into it. Then the air in the reactor was replaced with nitrogen, then the reactor was heated to 55°C under stirring, 0.04 parts by weight of potassium persulfate was added to make it react, the reaction temperature was controlled to be less than 73°C, and the temperature was lowered to below 60°C.
[0022] The pre-emulsified second monomer composition The monomer composition includes 41 parts by weight of styrene monomer, 7 parts by weight of acrylonitrile monomer, 2 parts by weight of n-butyl methacrylate, 4 parts by weight of ten Sodium dialkyldiphenyl ether disulfonate, 0.04 pa...
Embodiment 2
[0024] The air in the reactor equipped with a stirrer and a reflux condenser was replaced with nitrogen. Then, 100 parts by weight of deionized water and 4 parts by weight of sodium dodecyl diphenyl ether disulfonate were added, and stirred evenly. 40 parts by weight of styrene monomer, 7 parts by weight of acrylonitrile monomer, 3 parts by weight The n-butyl methacrylate monomer composition was put into it. Then the air in the reactor was replaced with nitrogen, then the reactor was heated to 55°C under stirring, 0.04 parts by weight of potassium persulfate was added to make it react, the reaction temperature was controlled to be less than 73°C, and the temperature was lowered to below 60°C.
[0025] The pre-emulsified second monomer composition The monomer composition includes 40 parts by weight of styrene monomer, 7 parts by weight of acrylonitrile monomer, 3 parts by weight of n-butyl methacrylate, 4 parts by weight of ten Sodium dialkyldiphenyl ether disulfonate, 0.04 pa...
Embodiment 3
[0027] The air in the reactor equipped with a stirrer and a reflux condenser was replaced with nitrogen. Then, 100 parts by weight of deionized water and 4 parts by weight of sodium dodecyl diphenyl ether disulfonate were added, and stirred evenly. 38 parts by weight of styrene monomer, 7 parts by weight of acrylonitrile monomer, 5 parts by weight The n-butyl methacrylate monomer composition was put into it. Then the air in the reactor was replaced with nitrogen, then the reactor was heated to 55°C under stirring, 0.04 parts by weight of potassium persulfate was added to make it react, the reaction temperature was controlled to be less than 73°C, and the temperature was lowered to below 60°C.
[0028] The pre-emulsified second monomer composition The monomer composition comprises 38 parts by weight of styrene monomer, 7 parts by weight of acrylonitrile monomer, 5 parts by weight of n-butyl methacrylate, 4 parts by weight of ten Sodium dialkyldiphenyl ether disulfonate, 0.04 p...
PUM
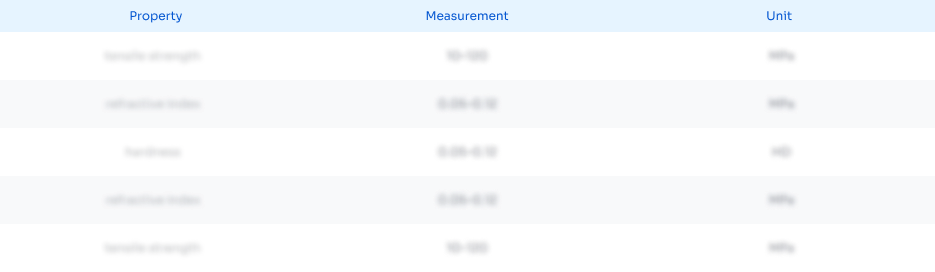
Abstract
Description
Claims
Application Information

- R&D
- Intellectual Property
- Life Sciences
- Materials
- Tech Scout
- Unparalleled Data Quality
- Higher Quality Content
- 60% Fewer Hallucinations
Browse by: Latest US Patents, China's latest patents, Technical Efficacy Thesaurus, Application Domain, Technology Topic, Popular Technical Reports.
© 2025 PatSnap. All rights reserved.Legal|Privacy policy|Modern Slavery Act Transparency Statement|Sitemap|About US| Contact US: help@patsnap.com