Medium frequency induction welding method of rail
A technology for induction welding and rails, which is applied to rails, welding equipment, rails, etc., can solve the problems of large influence of human factors, difficulty in realizing accurate measurement and control of rail temperature, and difficult quality control, so as to ensure the quality of welds and their Stability, convenient for automatic assembly line production, and realize the effect of automatic assembly line production
- Summary
- Abstract
- Description
- Claims
- Application Information
AI Technical Summary
Problems solved by technology
Method used
Image
Examples
Embodiment 1
[0035] As shown in the figure, the present invention adopts an intermediate frequency induction heating method, based on the principle of pressure welding, through welding upsetting to make the two rails to be welded into one body, which specifically includes the following steps (take U71Mn rail as an example):
[0036] 1. Preparation before welding. Grind the end surface of the rail 6 to be welded with a grinder, and use a clean file to manually fine file. The file cleaning agent uses carbon tetrachloride. The surface roughness of the polished rail end surface is Ra12.5 microns, and the end surface flatness and the tolerance of the perpendicularity between the end surface and the rail axis are 0.15 mm.
[0037] 2. Use the air pressure welding and crimping machine 2 to clamp the steel rail 6 to be welded, and adjust the relative position of the two steel rails 6 to be welded so that the end faces to be welded are aligned. The air pressure welding and crimping machine 2 is connecte...
Embodiment 2
[0049] The medium frequency induction welding method of the steel rail specifically includes the following steps (take U75V steel rail as an example):
[0050] 1. Preparation before welding.
[0051] 2. Clamp the rail 6 to be welded by the air pressure welding and crimping machine 2.
[0052] 3. Support the intermediate frequency sensor 3 on the two guide posts 201 of the air pressure welding and crimping machine 2, and make the intermediate frequency sensor 3 surround the welding end faces of the two steel rails 6 to be welded. Adjust the left, right, upper and lower gaps between the intermediate frequency inductor 3 and the steel rail 6 to be welded to 29mm.
[0053] 4. The intermediate frequency sensor 3 is connected with a water cooling system, and the power supply of the water cooling system is turned on to supply circulating cooling water to the intermediate frequency sensor 3.
[0054] 5. Rail pre-top.
[0055] 6. The intermediate frequency inductor 3 is used to heat the end surf...
Embodiment 3
[0062] The medium frequency induction welding method of the steel rail specifically includes the following steps (take PG4 rail as an example):
[0063] 1. Preparation before welding.
[0064] 2. Clamp the rail 6 to be welded by the air pressure welding and crimping machine 2.
[0065] 3. Support the intermediate frequency sensor 3 on the two guide posts 201 of the air pressure welding and crimping machine 2, and make the intermediate frequency sensor 3 surround the welding end faces of the two steel rails 6 to be welded. Adjust the left, right, upper and lower gaps between the intermediate frequency sensor 3 and the steel rail 6 to be welded to 31mm.
[0066] 4. The intermediate frequency sensor 3 is connected with a water cooling system, and the power supply of the water cooling system is turned on to supply circulating cooling water to the intermediate frequency sensor 3.
[0067] 5. Rail pre-top.
[0068] 6. The intermediate frequency inductor 3 is used to heat the end surface area ...
PUM
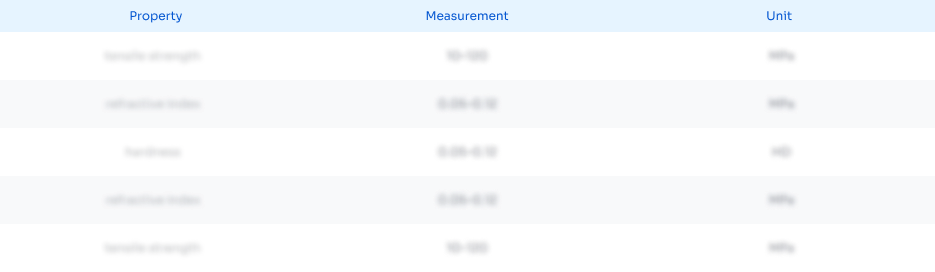
Abstract
Description
Claims
Application Information

- Generate Ideas
- Intellectual Property
- Life Sciences
- Materials
- Tech Scout
- Unparalleled Data Quality
- Higher Quality Content
- 60% Fewer Hallucinations
Browse by: Latest US Patents, China's latest patents, Technical Efficacy Thesaurus, Application Domain, Technology Topic, Popular Technical Reports.
© 2025 PatSnap. All rights reserved.Legal|Privacy policy|Modern Slavery Act Transparency Statement|Sitemap|About US| Contact US: help@patsnap.com