Disperse printing thickener and preparation method thereof
A thickening agent and printing technology, applied in the field of printing and dyeing auxiliaries, can solve the problems of unsatisfactory thickening effect, electrolyte resistance and poor hand feel of the disperse printing thickener, so as to improve the electrolyte resistance, easy to depaste, and beneficial to The effect of feel
- Summary
- Abstract
- Description
- Claims
- Application Information
AI Technical Summary
Problems solved by technology
Method used
Image
Examples
Embodiment 1
[0038] Under stirring at room temperature, 50 grams of acrylic acid was neutralized with 70 grams of liquid caustic soda, and 5.0 grams of potassium persulfate and 30 grams of deionized water were added and mixed to obtain a water phase. Take 100 grams of the above water phase, and add the water phase to 5 grams of sorbitan monooleate, 0.1 grams of diallyl phthalate, 5 grams of acrylamide, and methacrylamide under high-speed stirring. 5 grams, 3 grams of vinyl silicone oil, 1 gram of methacryloyloxyethyltrimethylammonium chloride, 3 grams of lauryl methacrylate and 55 grams of kerosene in the oil phase, high-speed 1000 rpm emulsification 30 minutes to obtain a stable pre-emulsion. Under the protection of nitrogen, raise the temperature of the pre-emulsion in the reactor to 50-60°C, the reaction will gradually start, and the temperature of the system will gradually rise. Cooling can be carried out to control the reaction temperature not to exceed 90°C. After 10 minutes of react...
Embodiment 2
[0040] Under stirring at room temperature, 50 grams of methacrylic acid was neutralized with 70 grams of liquid caustic soda, and 8.0 grams of potassium persulfate and 30 grams of deionized water were added and mixed to obtain an aqueous phase. Take 100 grams of the above-mentioned water phase, and add the water phase to 5 grams of sorbitan monostearate, 0.1 gram of divinylbenzene, 7 grams of styrene, 7 grams of ethyl acrylate, ethylene under high-speed stirring. In the oil phase composed of 4 grams of base silicone oil, 2 grams of methacryloyloxyethyltrimethylammonium chloride, 3 grams of myristyl methacrylate and 55 grams of gasoline, emulsify at a high speed of 1000 rpm for 30 minutes to obtain stable pre-emulsion. Under the protection of nitrogen, raise the temperature of the pre-emulsion in the reactor to 50-60°C, the reaction will gradually start, and the temperature of the system will gradually rise. Cooling can be carried out to control the reaction temperature not to ...
Embodiment 3
[0042] Under stirring at room temperature, 20 grams of acrylic acid and 30 grams of maleic acid were neutralized with 80 grams of liquid caustic soda, and 6.5 grams of ammonium persulfate and 35 grams of deionized water were added and mixed to obtain an aqueous phase. Take 100 grams of the above-mentioned water phase, and add the water phase under high-speed stirring to the already filled 5 grams of sorbitan monopalmitate, 0.2 grams of ethylene glycol diacrylate, 10 grams of ethyl methacrylate, acrylic acid In the oil phase composed of 5 grams of butyl ester, 5 grams of vinyl silicone oil, 3 grams of methacryloyloxyethyltrimethylammonium chloride, 3 grams of cetyl methacrylate and 55 grams of white oil, the high speed is 1200 rpm Separate emulsification for 30 minutes to obtain a stable pre-emulsion. Under the protection of nitrogen, raise the temperature of the pre-emulsion in the reactor to 50-60°C, the reaction will gradually start, and the temperature of the system will gr...
PUM
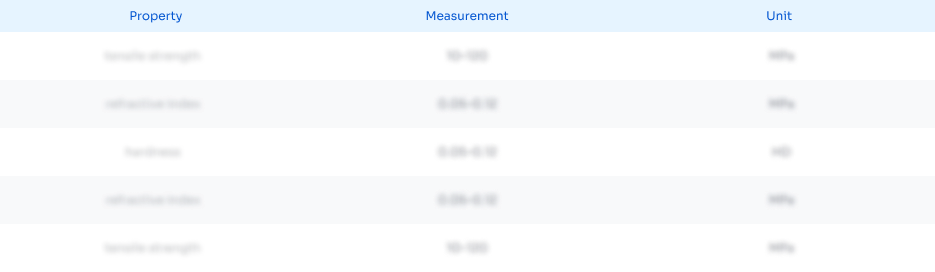
Abstract
Description
Claims
Application Information

- Generate Ideas
- Intellectual Property
- Life Sciences
- Materials
- Tech Scout
- Unparalleled Data Quality
- Higher Quality Content
- 60% Fewer Hallucinations
Browse by: Latest US Patents, China's latest patents, Technical Efficacy Thesaurus, Application Domain, Technology Topic, Popular Technical Reports.
© 2025 PatSnap. All rights reserved.Legal|Privacy policy|Modern Slavery Act Transparency Statement|Sitemap|About US| Contact US: help@patsnap.com