Method for preparing nickelous carbonate by utilization of waste ammonia decomposition catalyst
A catalyst and ammonia decomposition technology, applied in the direction of nickel carbonate, etc., can solve the problems of nickel resource shortage, low nickel carbonate performance index, high impurity content, etc., and achieve low loss, high nickel leaching rate, and high product purity.
- Summary
- Abstract
- Description
- Claims
- Application Information
AI Technical Summary
Problems solved by technology
Method used
Image
Examples
Embodiment 1
[0032] Take 100kg of waste ammonia decomposition catalyst, ball mill, and roast the material after ball milling at 500°C for 2 hours. After roasting, it is leached with concentrated sulfuric acid, wherein the mass ratio of catalyst to concentrated sulfuric acid is 1:4, a small amount of sodium chlorate is added during the reaction, and the air stirrer is turned on at the same time, the reaction temperature is controlled at 80-85°C, and the pH value is controlled at 0.5- 1.0, reacted for 3 hours. The amount of sodium chlorate added is 15% of the Ni metal molar content ratio in the spent catalyst, and the nickel leaching rate is 92%. Plate and frame filter press, add sodium carbonate solid to the filtrate to adjust the pH value to 4.0, plate and frame press filter, add sodium fluoride solid to the filtrate, the molar ratio of sodium fluoride to magnesium metal is 1.5, heat to 90°C, react for 1 hour, plate and frame Press filtration, use sulfonated kerosene and P204 with a volum...
Embodiment 2
[0034] Get 100kg of waste ammonia decomposition catalyst, ball mill, and roast the material after ball milling at 600°C for 3 hours. After roasting, it is leached with concentrated hydrochloric acid, wherein the mass ratio of catalyst to acid is about 1:4. During the reaction, a small amount of sodium chlorate is added and the air stirrer is turned on at the same time. The reaction temperature is controlled at 75-80°C, and the pH value is controlled at 0.5-1.0. React for 5 hours. The amount of sodium chlorate added is 20% of the Ni metal molar ratio in the spent catalyst, and the nickel leaching rate is 91%. Plate and frame filter press, add sodium carbonate solid to the filtrate to adjust the pH value to 4.0, plate and frame press filter, add sodium fluoride solid to the filtrate, the molar ratio of sodium fluoride to magnesium metal is 1.3, heat to 80°C, react for 1 hour, plate and frame Press filtration, use sulfonated kerosene and P204 with a volume ratio of 3.8:1 to extr...
PUM
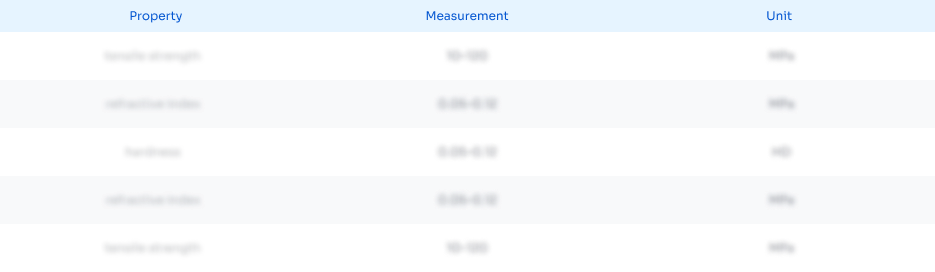
Abstract
Description
Claims
Application Information

- R&D
- Intellectual Property
- Life Sciences
- Materials
- Tech Scout
- Unparalleled Data Quality
- Higher Quality Content
- 60% Fewer Hallucinations
Browse by: Latest US Patents, China's latest patents, Technical Efficacy Thesaurus, Application Domain, Technology Topic, Popular Technical Reports.
© 2025 PatSnap. All rights reserved.Legal|Privacy policy|Modern Slavery Act Transparency Statement|Sitemap|About US| Contact US: help@patsnap.com