Calcium aluminate slag containing sodium oxide and titanium oxide
A technology containing sodium oxide and calcium aluminate is applied in the fields of calcium aluminate slag containing titanium oxide and sodium oxide, which can solve the problems of low alumina leaching rate from the slag, and achieve the effects of improving economic benefits and increasing production.
- Summary
- Abstract
- Description
- Claims
- Application Information
AI Technical Summary
Problems solved by technology
Method used
Examples
Embodiment 1
[0009] Embodiment 1: slag composition is proportioned by mass percentage, wherein, Na 2 O1.96%, TiO 2 3.93%, CaO56.60%, SiO 2 20.64%, Al 2 o 3 16.87%, totaling 100%. Al in the prepared material 2 o 3 with SiO 2 The mass ratio of CaO is 0.8; the total amount of CaO added meets the three requirements, first of all, it meets the requirements of SiO 2 The reaction generates 2CaO. SiO 2 requirements, and secondly to meet the requirements of Al 2 o 3 The reaction produces 12CaO. 7Al 2 o 3 The amount of CaO required, but also to meet the requirements of TiO 2 Calcium content, for TiO 2 The mass percentage of CaO allocated is 2.24%, and this part of CaO and TiO 2 The mass ratio of the substance is converted into a molar ratio of 0.8.
[0010] The above-mentioned materials are smelted at 1550°C for 1 hour, then cooled to 1200°C at a cooling rate of 4-5°C / min, and then naturally cooled to room temperature to obtain calcium aluminate slag.
[0011] The alumina leaching ...
Embodiment 2
[0012] Embodiment 2: slag composition is proportioned by mass percentage, wherein, Na 2 O1.87%, TiO 2 5.61%, CaO56.76%, SiO 2 19.67%, Al 2 o 3 16.08%, totaling 100%. Al in the prepared material 2 o 3 with SiO 2 The mass ratio of CaO is 0.8; the total amount of CaO added meets the three requirements, first of all, it meets the requirements of SiO 2 The reaction generates 2CaO. SiO 2 requirements, and secondly to meet the requirements of Al 2 o 3 The reaction produces 12CaO. 7Al 2 o 3 The amount of CaO required, but also to meet the requirements of TiO 2 Calcium content, for TiO 2 The mass percentage of CaO allocated is 5.25%, and this part of CaO and TiO 2 The mass ratio is converted into a material molar ratio of 1.25.
[0013] The above materials were smelted and cooled under the same process conditions as in Example 1 to obtain calcium aluminate slag.
[0014] Alumina leaching condition is identical with embodiment 1, Al 2 o 3 The leaching rate was 84.1%....
Embodiment 3
[0015] Embodiment 3: slag composition is proportioned by mass percentage, Na 2 O3.82%, TiO 2 3.82%, CaO54.50%, SiO 2 18.94%, Al 2 o 3 18.94%, for a total of 100%. Al in the prepared material 2 o 3 with SiO 2 The mass ratio of the substance is 1.0; the total amount of CaO added meets the three requirements, first of all, it meets the requirements of SiO 2 The reaction generates 2CaO. SiO 2 requirements, and secondly to meet the requirements of Al 2 o 3 The reaction produces 12CaO. 7Al 2 o 3 The amount of CaO required, but also to meet the requirements of TiO 2 Calcium content, for TiO 2 The CaO mass percentage that is allocated is 1.4%, this part CaO and TiO 2 The mass ratio of the substance is converted into a molar ratio of 0.5.
[0016] The above materials were smelted and cooled under the same process conditions as in Example 1 to obtain calcium aluminate slag.
[0017] Alumina leaching condition is identical with embodiment 1, Al 2 o 3 The leaching rate...
PUM
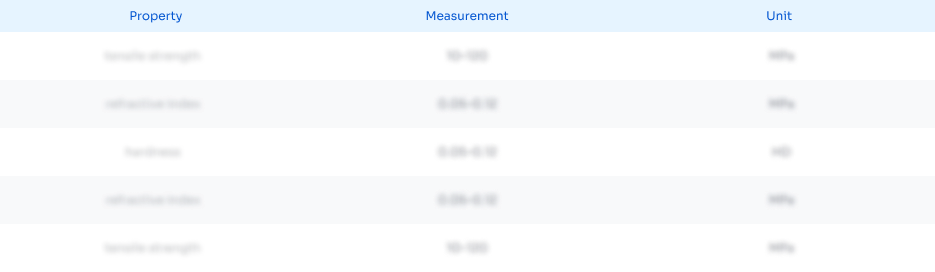
Abstract
Description
Claims
Application Information

- R&D
- Intellectual Property
- Life Sciences
- Materials
- Tech Scout
- Unparalleled Data Quality
- Higher Quality Content
- 60% Fewer Hallucinations
Browse by: Latest US Patents, China's latest patents, Technical Efficacy Thesaurus, Application Domain, Technology Topic, Popular Technical Reports.
© 2025 PatSnap. All rights reserved.Legal|Privacy policy|Modern Slavery Act Transparency Statement|Sitemap|About US| Contact US: help@patsnap.com